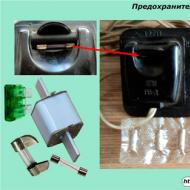
Cистема питания двигателя от газобаллонной установки. Система питания двигателя газобаллонного автомобиля Система питания двигателя газом
Введение
Система питания автомобиля с газобаллонным оборудованием
1 Назначение ГБО
2 Классификация ГБО
3 Устройство ГБО
4 Принцип работы системы питания автомобиля Renault Logan
5 Техническое обслуживание ГБО
6 Ремонт ГБО
6.1 Виды ремонта
6.2 Ремонт деталей ГБО
7 Техническая планировка участка по ремонту ГБО
8 Техника безопасности при ТО и ремонте ГБО
9 Охрана труда на предприятии
Заключение
Литература
Приложения
Введение
В наши дни, автомобиль является самым распространённым видом транспортного средства. Если совсем недавно, буквально 10-20 лет назад дороги крупных городов были широки и свободны, а сейчас автомобилисту приходится по несколько часов стоять в пробке что бы добраться до пункта назначения. Тем не менее, с каждым днём количество автомобилей растёт, а производители то и дело пытаются внедрить новые технологии, которые превращают знакомый нам автомобиль, в умный гаджет который умеет думать и самостоятельно действовать в той или иной ситуации.
И если первые автомобили были совсем не безопасными, а иметь их могли только состоятельные люди, то теперь существуют разнообразные классы автомобилей, нацеленные на разные кошельки и потребности. Естественно, каждый человек стремится и хочет купить дорогой автомобиль, имеющий именитую родословную, качественные материалы кузова и богатое оснащение салона. Элитные автомобили имеют не только солидную внешность, но и оснащены самыми передовыми технологиями. А вот бюджетные авто получают только самые необходимые примочки, но как и все другие они выполняют своё прямое назначение - доставляют своего хозяина из пункта «А» в пункт «Б» и обратно.
Огромное количество людей уже оценили все преимущества передвижения на автомобиле и поэтому не желают расставаться с этим удобством ни на мгновение. Поэтому уже сегодня, большую популярность набирают прокаты автомобилей. Они конечно появились уже давно, но в основном данной услугой пользовались только состоятельные люди. Теперь же, аренда машины бизнес класса доступна любому человеку.
Мир не стоит на месте, а вместе с ним и не стоим на месте мы сами.
Автомобили превращаются в неотъемлемую часть нашей жизни, впитывают в себя все
необходимые функции для комфортной езды на дальние расстояния, умеют переводить
большие грузы, могут быть незаметными в городском потоке или лететь навстречу
ветру, достигая неимоверные скоростных показателей. Семейные, спортивные,
внедорожники, грузовые, городские, хетчбеки, седаны, универсалы, пикапы - каким
бы ни был автомобиль, он помогает нам и без него в наше время невозможно
обойтись.
. Система питания автомобиля с газобаллонным оборудованием
.1 Назначение ГБО
Система питания газобаллонного автомобиля служит для хранения запаса топлива, очистки топлива и воздуха, приготовления горючей смеси, подачи ее в цилиндры двигателя и выпуска отработавших газов
1.2 Классификация ГБО
В актуальной технической литературе отсутствует единая методика классификации ГБО различных поколений, практически все монтажники ГБО руководствуются условной системой классификации газового оборудования. Условное разделение ГБО на поколения создает удобство при профессиональном общении и помогает специалистам по монтажу четко определять конструктивные особенности того или иного типа газового оборудования.
Первое поколение
Системы с вакуумным управлением и механическим дозатором газа, которые устанавливают на бензиновые карбюраторные и простые инжекторные автомобили. В первом поколении используются как вакуумные, так и электронные газовые редуктора. Без лямбда-зонда.
Описание
Это традиционные устройства со смесителем газа. Принципиальное различие вакуумного редуктора от электронного заключается в запорном элементе разгрузочной камеры: в вакуумном эту функцию выполняет вакуумная мембрана к которой подаётся разрежение от впускного коллектора:
Двигатель работает - есть вакуум - редуктор открыт
Двигатель заглушен - вакуума нет - редуктор закрыт
Плюсы
· простое, недорогое решение
· может применяться и на простых инжекторных двигателях без обратной связи
Минусы
· не соответствует современным нормам безопасности
· это можно сказать «прошлый век», на котором основываются последующие поколения газового оборудования
Второе поколение
Механические системы, дополненные электронным дозирующим устройством, работающим по принципу обратной связи с датчиком содержания кислорода.
Описание
Устанавливаются на автомобили, оснащенные инжекторным двигателем, с лямбда-зондом и нейтрализатором и каталитическим нейтрализатором отработавших газов ("катализатором"). Это традиционные устройства со смесителем газа, дополнительно оснащенные дозаторами газа.
Для поддержания правильного состава газо-воздушной смеси Лямбда-контроллеры используют сигнал от штатного Лямбда-зонда автомобиля, а так же сигнал положения дроссельной заслонки и датчика оборотов двигателя, для оптимизации топливно-воздушной смеси на переходных режимах работы двигателя.
Плюсы
· дополнительное оснащение дозаторами газа
· гарантирует поддержание экологических требований Евро 1
Минусы
· большая вероятность «хлопков»
· сокращается срок эксплуатации свечей зажигания и воздушного фильтра
· токсичность отработавших газов автомобилей, оснащенных такими системами, как правило, находится на уровне норм ЕВРО-1, которые действовали в Европе до 1996 года, и лишь в отдельных случаях приближаются к нормам ЕВРО-2
Третье поколение
На 80% схожа с ГБО 2-го поколения. Конструктивной особенностью данной установки является электронная дозировка подачи топлива.
Описание
Производится индивидуальная подача газа в отдельные цилиндры дозирующим устройством (газовым инжектором), имеющим одноуровневое управление порцией газа, который управляется электронным блоком. Газ подается во впускной коллектор с помощью механических форсунок, которые открываются за счет избыточного давления в магистрали подачи газа.
Установка ГБО третьего поколения на инжекторные автомобили отличается тем, что вместо бензоклапана для отсечения подачи бензина используется эмулятор форсунок. Когда подается газ, этот эмулятор имитирует работу бензиновых форсунок, чтобы штатный компьютер не перешел в аварийный режим. По этой же причине нужно устанавливать эмулятор лямбда-зонда.
Плюсы
· встроенный электронный блок питания обеспечивает нужную газовоздушную подачу
· работа осуществляется от подачи сигналов с датчиков мотора (Лямбда-зонд, RPM, TPS, MAP)
· особая система подачи газа - с помощью параллельного впрыска
· газовый мотор и ЭБУ (электронный блок управления)
Минусы
· небольшая скорость реакции на изменение режима езды
· невысокая скорость реакции на корректировку смеси
· не соответствие экологическим требованиям Евро-3
Четвертое поколение
Это системы с распределенным синхронизированным впрыск газа. Это новейшие и наилучшие из известных сегодня решений в восточной Европе: отдельное управление подачей газа (форсунками газа) для каждого цилиндра, которые управляются более совершенным электронным блоком.
Описание
Газовая установка 4-го поколения отличается от предыдущих тем, что является точной копией бензинового инжектора, а именно: каждый цилиндр имеет свою форсунку, подающую рассчитанный необходимый для работы данного цилиндра впрыск газа. А работа форсунок контролируется ЭБУ. При этом ЭБУ принимает непосредственное участие в работе двигателя на ГБО, работая с множеством датчиков необходимых для корректной работы двигателя на газу.
Данный вид газового впрыска полностью исключает вероятность «хлопков», требует менее внимания к свечам зажигания и воздушному фильтру. Расход газа максимально приближен к расходу бензина, сохраняя при этом динамику автомобиля.
Плюсы
· функция автоматического перехода с бензина на газ, и наоборот (когда газ в баллоне закончился)
· совместима с экологическими требованиями Euro 3, а также с системами бортовой диагностики OBDІІ, EOBD
· является точной копией бензинового инжектора
· исключена вероятность «хлопков»
· ошибки при монтаже практически не возможны, так как все соединительные детали унифицированы.
Пятое поколение
Предназначено для использования в любых инжекторных автомобилях и совместимо с экологическими требованиями Евро-3, Евро-4 а так же системами бортовой диагностики OBD II, OBD III и EOBD.
Описание
В отличии от системы 4 поколения, в системах 5 поколения, газ поступает в цилиндры в жидкой фазе. Для этого в баллоне находится "газо насос", который обеспечивает циркуляцию жидкой фазы газа из баллона через рампу газовых форсунок с клапаном обратного давления обратно в баллон. Системы 5 поколения используют вычислительные мощности и топливные карты, заложенные в штатный контроллер а/м, и вносят лишь необходимые поправки для адаптации газобаллонного оборудования к бензиновой топливной карте. 5 поколение характеризует наличие отдельных электромагнитных форсунок впрыска газа в каждый цилиндр т. е. полностью аналогично бензиновой системе. Фазу и дозировку впрыска определяет штатный бензиновый контроллер а/м. Важным плюсом систем 3, 4 и 5 поколения является функция автоматического перехода с газового топлива на бензиновое.
Плюсы
· газ поступает в цилиндры в жидкой фазе
· отдельные электромагнитные форсунки впрыска газа в каждый цилиндр
· отсутствие потери мощности и отсутствие повышенного расхода газа
· возможность запуска двигателя на газе при любых отрицательных температурах
Минусы
· высокая чувствительность к грязному газу
· низкая ремонтопригодность
· высокая сложность
.3 Устройство ГБО
Газовую топливную аппаратуру можно устанавливать на любой модели легковых автомобилей отечественного и иностранного производства, оснащённых карбюраторными двигателями или двигателями с системой впрыска топлива и электронным управлением, если конструкция позволяет разместить в багажнике цилиндрический или тороидальный баллон с газом. Конструктивные решения комплектующих устройств газобаллонной аппаратуры (ГБА) отличаются большим разнообразием в зависимости от типов двигателей, для которых они предназначены, и от заводов-изготовителей, их производящих.
Газовое оборудование автомобиля размещают в трех местах: в моторном отсеке, салоне и багажном отсеке.
В моторном отсеке автомобиля устанавливают:
Редуктор-испаритель газа;
смеситель;
электромагнитный газовый клапан;
электромагнитный бензиновый клапан.
В салоне на приборной панели устанавливают:
Переключатель видов топлива «Газ - Бензин» с блоком индикации режимов «Газ - Бензин» и количества топлива в газовом баллоне;
предохранитель.
В багажном отсеке устанавливают:
Газовый баллон с запорно-предохранительной арматурой;
выносное заправочное устройство.
За основу взято устройство системы питания автомобиля Renault Logan с ГБО 3-го поколения
ГАЗОВЫЙ БАЛЛОН (см. Приложение А,рис.1.) - стальной резервуар, предназначенный для хранения сжиженного нефтяного газа при температуре от - 40° до + 45 °С. На легковом автомобиле он крепится в багажном отделении или в нише для запасного колеса, а на малотоннажных автомобилях - на раме. Газовый баллон имеет цилиндрическую или тороидальную форму Различные объемы и геометрические размеры позволяют выбрать оптимальный вариант размещения баллона в багажнике автомобиля. Баллон снабжен вентиляционной коробкой с герметически закрывающейся крышкой. Под крышкой расположены заправочный и расходный вентили, шкала со стрелкой, показывающей уровень газа в баллоне, заправочная чашка.
БЛОК ЗАПОРНО-КОНТРОЛЬНОЙ И ПРЕДОХРАНИТЕЛЬНОЙ АРМАТУРЫ (см. Приложение А, рис.2.) -устанавливают на унифицированном фланце газовогобаллона с использованием прокладки, обеспечивающей герметичностьсоединения. Он является приемным устройством, при заполнении баллонасжиженным нефтяным газом и обеспечивает подачу последнего в магистральгазопровода. Блок включает в себя входной штуцер и заправочный вентиль собратным клапаном, расходный штуцер и расходные вентили жидкой ипаровой фаз, ограничительный механизм уровня заправки баллона(мультиклапан). Блок закрыт герметичным кожухом, надежно отделяющим егосодержимое от внутреннего объема автомобиля. Вентиляция внутреннегопространства кожуха осуществляется через дренажную трубку, выведенную запределы кузова автомобиля.
ВЫНОСНОЕ ЗАПРАВОЧНОЕ УСТРОЙСТВО (см. Приложение Б,рис.3.), предназначено для заправки ГСН, крепится на кронштейне (7) гайкой (8) под задним бампером легкового автомобиля. Оно подсоединяется к заправочному трубопроводу через штуцер (10). Заправочный пистолет газовой колонки присоединяется к корпусу (3) с уплотняющей резиновой прокладкой (2). Газ, поступающий под давлением, открывает клапан (6) и заполняет газовый баллон. После окончания заправки клапан герметично закрывается.
ГАЗОПРОВОД И СОЕДИНИТЕЛЬНЫЕ ЭЛЕМЕНТЫ
. Газопровод проходит под полом
автомобиля вдали от выхлопных труб. От соприкосновения с деталями кузова он
защищен хлорвиниловыми или резиновыми трубками. Трубопроводы закрепляют на
кузове автомобиля специальными скобами при помощи саморезов с интервалом не
более 800 мм. Газопровод высокого давления на всем протяжении от баллона до
электромагнитного клапана газа и от него до редуктора-испарителя выполнен из
меди или из нержавеющей стали с заводской развальцовкой (рис. 4.). Если
газопровод изготовлен из стали, то его присоединение к узлам аппаратуры
осуществляется при помощи упорной накидной гайки. Такое соединение допускает
многократную разборку, но при затяжке необходимо избегать чрезмерных усилий во
избежание отрыва донышка накидной гайки.
Рис.4. Трубопроводы из нержавеющей стали
На концах трубопровода предусматривают компенсационные кольца. Трубку изгибают с образованием кольца диаметром 50-80 мм, что предохраняет трубопровод от поломки под действием вибрации. Герметичность газопровода высокого давления (рис.5.) обеспечивает ниппельное соединение типа конусная муфта. Такое соединение включает в себя трубопровод (3), конусную муфту (1), упорную гайку (2) и присоединяемую деталь (штуцер). Герметичность достигается за счет конусной муфты (1), изготавливаемой из латуни. Такое соединение допускает многократную разборку с заменой конусной муфты новой. Муфта должна плотно сидеть на трубке на расстоянии 2-3 мм от ее торца.
В трубопроводах низкого давления для соединения газового редуктора со
смесителем используют резиновые шланги из бензомаслостойкой резины. Шланговые
соединения на штуцерах крепятся винтовыми хомутами типа «Норма».
Рис.5. Беспрокладочные соединения трубопроводов с помощью конусной муфты:
а - конусная муфта; б, в - соединение трубопровода; 1 - конусная муфта
(ниппель); 2 - гайка; 3 - трубка; 4 - присоединяемая деталь (штуцер)
КЛАПАНЫ БЕНЗИНОВЫЕ И ГАЗОВЫЕ- устанавливают с целью исполнения команд, которые управляют подачей бензина или газа в системах питания автомобилей, оборудованных газобаллонной аппаратурой. В отдельных случаях клапаны конструктивно объединяют с фильтрами, которые очищают поступающее в систему топливо.
Электромагнитный газовый клапан (Приложение Б,В,рис.6,7) - служит для открытия канала подачи газа в редуктор и его перекрытия при работе на бензине (управляется дистанционно из салона автомобиля посредством переключателя «Газ» - «Бензин»). Фильтры не требуют регулярного обслуживания: достаточно промывки или замены. В некоторых конструкциях очищать фильтры следует каждые 30 ООО км пробега автомобиля. При включенном зажигании и установке переключателя в положение «Газ» клапан открывается, и газ по трубопроводу высокого давления поступает в редуктор-испаритель. При включенном зажигании клапан находится в положении «Закрыт».
Электромагнитный бензиновый клапан (Приложение В,Г,рис.8,9) - служит для открытия (закрытия) канала подачи бензина в карбюратор, одновременно перекрывается подача газа. В нижней части клапана предусмотрен винт (кран) для механического (ручного) открывания клапана. В случае выхода из строя электронного блока управления газовым оборудованием этот винт следует ввернуть в клапан (или повернуть кран), чтобы можно было продолжить движение.
ЭЛЕКТРОННЫЙ БЛОК УПРАВЛЕНИЯ (ЭБУ) - многофункциональное электронное устройство, управляющее подачей газа на автомобилях, которые оборудованы лямбда-зондом и каталитическим нейтрализатором. Обеспечивает стехиометрический состав смеси во всех режимах работы двигателя. ЭБУ автоматически закрывает запорные клапаны в случае аварийного повреждения газовой магистрали или при остановке двигателя.
ЛЯМБДА-ЗОНД - датчик содержания несгоревшего кислорода в отработавших газах. Устанавливается в системе выпуска перед каталитическим нейтрализатором (обычно в приемной трубе глушителя). По информации от лямбда-зонда блок управления (ЭБУ) двигателем поддерживает стехиометрический состав горючей смеси.
РЕДУКТОР-ИСПАРИТЕЛЬ
- предназначен для превращения жидкой фазы газа в паровую и
подачи паровой фазы в смеситель. Редукторы-испарители играют важную роль в
работе газобаллонного оборудования, поэтому им следует уделить особое внимание.
.4 Принцип работы системы питания автомобиля Renault Logan
Сжиженный нефтяной газ (пропан-бутан) под давлением поступает из баллона в газовую магистраль высокого давления. Расход газа из баллона происходит посредством мультиклапана, через который также осуществляется заправка с помощью выносного заправочного устройства. По магистрали газ в жидкой фазе попадает в газовый клапан-фильтр, который очищает газ от взвесей и смолистых отложений и перекрывает подачу газа при выключении зажигания или при переходе на бензин.
Далее очищенный газ по трубопроводу поступает в редуктор-испаритель, где давление газа понижается с шестнадцати атмосфер до одной. Интенсивно испаряясь, газ охлаждает редуктор, поэтому последний присоединяется к системе водяного охлаждения двигателя. Циркуляция тосола позволяет избежать обмерзания редуктора и его мембран. Под действием разряжения, создаваемого во впускном коллекторе работающего двигателя, газ из редуктора по шлангу низкого давления через дозатор поступает в смеситель, установленный между воздушным фильтром и дроссельными заслонками карбюратора. Иногда вместо установки смесителя производится непосредственная врезка газовых штуцеров в карбюратор.
Управление режимами работы (на газе или на бензине) осуществляется с помощью переключателя видов топлива установленного на панели приборов. При выборе позиции "ГАЗ" переключатель открывает электромагнитный газовый клапан и отключает электромагнитный бензиновый клапан. И, наоборот, при переходе с газа на бензин, переключатель закрывает газовый клапан и открывает бензиновый. С помощью светодиодов переключатель позволяет контролировать, какое топливо используется в данный момент. Переключатель может быть оснащен указателем уровня топлива в баллоне (для этого мультиклапан должен быть оснащен сенсором уровня топлива).
.5 Техническое обслуживание ГБО
Для газового оборудования газобаллонных автомобилей предусмотрены ежедневное (ЕО), первое (ТО-1), второе (ТО-2) и сезонное (СО) технические обслуживания. Выполнение работ по ТО-1 и ТО-2 газовой системы питания проводится в сроки, установленные для ТО-1 и ТО-2 автомобиля. При этом проведение работ ТО-2 совмещают с очередным ТО-1, а сезонное обслуживание - с ТО-2.
Ежедневное техническое обслуживание выполняют перед выездом автомобиля и после возвращения его в гараж. Перед выездом проводят контрольные работы. Внешним осмотром проверяют техническое состояние газового баллона, деталей крепления газового оборудования, герметичность соединений всей газовой магистрали и показания контрольно-измерительных приборов (манометр, показывающий давление газа в редукторе, указатель уровня газа в баллоне).
После возвращения автомобиля в гараж проводят уборочно-моечные работы системы питания, проверяют техническое состояние газового редуктора и герметичность соединений газовой магистрали высокого давления.
В газовом редукторе на слух или с помощью прибора ПГФ-2М1-ИЗГ определяют герметичность клапана второй ступени и сливают масляный конденсат. Ежедневный слив конденсата необходим, так как скопление его на мембране второй ступени редуктора нарушает нормальную работу двигателя.
Герметичность системы проверяют в рабочем состоянии, т. е. при заполнении ее сжиженным газом. Места утечек определяют с помощью мыльного (пенного) раствора или прибором ПГФ-2М1-ИЗГ.
В зимнее время при заполнении системы охлаждения водой ее сливают из полости испарителя.
Первое техническое обслуживание газовой системы питания включает в себя контрольно-диагностические и крепежные работы, которые выполняют при ЕО, а также смазочно-очистительные работы, к которым относятся очистка фильтрующих элементов газовых фильтров и смазка резьбовых штоков магистрального наполнительного и расходных вентилей.
После выполнения отмеченных выше работ при ТО-1 проверяют герметичность газовой системы при давлении 1,6 МПа воздухом или инертным газом и работу двигателя на газовом топливе. В этом случае замеряют, а при необходимости и регулируют содержание окиси углерода в отработавших газах, определяют надежность пуска двигателя и устойчивость его работы на холостом ходу при различной частоте вращения коленчатого вала.
При втором техническом обслуживании проверяют состояние и крепление газового баллона к кронштейнам, кронштейнов к лонжеронам рамы, карбюратора к впускному патрубку и впускного патрубка к смесителю. В объем контрольно-диагностических и регулировочных работ входят проверка и установка угла опережения зажигания при работе двигателя на газе, проверка и регулировка газового редуктора, смесителя газа и испарителя.
В редукторе проверяют регулировку первой и второй ступеней, работу дозирующе-экономайзерного устройства и герметичность разгрузочного устройства.
В смесителе проверяют состояние и действие приборов воздушной и дроссельной заслонок, в испарителе - герметичность и засоренность газовой и водяной полостей.
Сезонное обслуживание газового оборудования по периодичности разделяется на три вида. К первому относятся работы, которые подлежат выполнению через 6 мес, ко второму - работы, проводимые один раз в год, к третьему - работы, выполняемые один раз в два года.
Через 6 мес. проверяют срабатывание предохранительного клапана газового баллона, продувают газопроводы сжатым воздухом и проверяют работу ограничителя максимальной частоты вращения коленчатого вала двигателя.
К работам, проводимым один раз в год, относится ревизия газовой аппаратуры, магистрального вентиля, манометра и арматуры баллона. Для этого газовый редуктор, смеситель газа, испаритель, магистральный вентиль демонтируют с автомобиля, разбирают, очищают, промывают, регулируют и при необходимости заменяют негодные детали.
Перед проведением ревизии газовой арматуры баллон полностью освобождают от газа. После этого снимают крышки наполнительного и расходных вентилей, вентиля максимального наполнения (не вывертывая корпусов из газового баллона) и проверяют состояние их деталей. Предохранительный клапан также снимают с баллона, регулируют на стенде и пломбируют.
Работы, проводимые раз в год, выполняют при подготовке автомобиля к зимней эксплуатации.
К специальной операции, выполняемой один раз в два года, относится освидетельствование газового баллона. При освидетельствовании проводятся гидравлические испытания, во время которых определяют прочность баллона. Во время пневматических испытаний определяют герметичность соединений баллона с арматурой. После испытаний газовый баллон окрашивают и наносят клеймо со сроком следующего освидетельствования.
При техническом обслуживании системы питания газобаллонных автомобилей кроме работ по газовому оборудованию выполняют работы и по резервной (бензиновой) системе питания. Периодичность и характер этих работ принципиально не отличаются от работ, выполняемых по системе питания автомобилей с карбюраторными двигателями, которые рассмотрены ранее.
Наличие у газобаллонных автомобилей газовой и бензиновой систем питания увеличивает трудоемкость работ по их техническому обслуживанию и текущему ремонту.
Проверка и регулировка газовой аппаратуры
Газовую аппаратуру системы питания проверяют и регулируют на специальных стендах или с помощью универсальных приборов и различных приспособлений без снятия с автомобиля. Часть регулировок выполняют во время работы двигателя на газе, другую часть - при неработающем двигателе с системой питания, заполненной воздухом или инертным газом под давлением 1,6 МПа.
В редукторе газа при неработающем двигателе регулируют давление в первой ступени, ход клапана второй ступени и проверяют герметичность разгрузочного и экономайзерного устройства.
Давление в первой ступени редуктора регулируют изменением положения регулировочного болта 14 (см. Приложение Д,рис.10.) и контролируют по манометру редуктора. При завертывании регулировочного болта давление будет увеличиваться, при отвертывании - уменьшаться. Регулировку прекращают при установлении в первой ступени давления 0,15 - 0,20 МПа.
Отрегулированный редуктор проверяют на герметичность закрытия клапана первой ступени. Для этого кратковременным нажатием на шток 11 (см. Приложение Е,рис.11.) редуктора открывают клапан второй ступени и выпускают из полости первой ступени воздух, снижая давление. При закрытии клапана второй ступени стрелка манометра должна указать заданное давление. Допускается медленное возрастание давления, но не более чем на 0,02 МПа и в то же время, не превышающее 0,2 МПа, после чего давление в камере должно сохраняться в интервале не менее 2 млн.
Клапан второй ступени редуктора регулируют на максимальное открытие, при котором не нарушается герметичность его в закрытом положении. Для регулировки снимают крышку 3 люка, ослабляют контргайку 4 и отвертывают регулировочный винт 5 до начала пропуска газа. Затем завертывают винт на ¼- ½оборота и затягивают контргайку. Регулировку клапана выполняют отверткой и специальным ключом (Приложение Е,рис.12).
После регулировки проверяют герметичность закрытия и ход клапана. Герметичность определяют на слух или по пузырькам воздуха, выходящим из шланга, один конец которого соединен со штуцером системы холостого хода на редукторе, а другой опущен в сосуд с водой на глубину не более 3 мм.
Величину хода клапана определяют по перемещению штока редуктора. Для этой проверки выпускают воздух из редуктора и нажатием на шток до отказа замеряют его ход приспособлением с мерной линейкой (см. Приложение Е,рис.11.). Нормальная величина открытия клапана второй ступени обеспечивается при ходе штока 11 не менее 8 мм.
Герметичность разгрузочного и экономайзерного устройств проверяют при отсутствии давления воздуха в системе питания. Для этого от всасывающего трубопровода снимают шланг, соединяющий его с редуктором, и через него отсасывают воздух в устройствах до создания разрежения не менее 266 Па. Разгрузочное и экономайзерное устройства считаются герметичными, если величина разрежения в них сохраняется в интервале 5 мин.
Давление во второй ступени редуктора регулируют регулировочным стаканом 9 (см. Приложение Е,рис.11.), а контроль давления ведут по водяному пьезометру, который подсоединяют через тройник в систему холостого хода. При отвертывании стакана давление в камере второй ступени уменьшается, при ввертывании - увеличивается. Регулировку выполняют во время работы двигателя на холостом ходу с частотой вращения коленчатого вала 500- 600 об/мин. Правильно отрегулированный редуктор на этом режиме работы двигателя создает избыточное давление его второй ступени 70-80 Па.
В газовом смесителе СГ-250 систему холостого хода регулируют двумя винтами, регулирующими подачу газа, и упорным винтом, ограничивающим закрытие дроссельных заслонок. Винтами подачи газа регулируют две камеры одновременно: при отвертывании горючая смесь обогащается, а при завертывании - обедняется.
Предварительную регулировку проводят на неработающем двигателе отвертыванием верхнего винта подачи газа на три оборота, а нижнего - на пол-оборота. Затем на работающем и полностью прогретом двигателе выполняют окончательную регулировку. Для этого при открытой крышке патрубка ввода газа в смеситель верхним винтом устанавливают такую общую подачу газа в систему холостого хода, при которой частота вращения коленчатого вала двигателя составляет 1300- 1400 об/мин.
После этого крышку патрубка закрывают и упорным винтом устанавливают наименьшее открытие дроссельных заслонок, при котором двигатель будет работать устойчиво. Затем начинают обеднять смесь, завертывая нижний винт подачи газа до тех пор, пока двигатель не начнет работать с явными перебоями, после чего вывертывают винт на 1/16 оборота.
Регулировку системы холостого хода в газовом смесителе СГ-250 можно совместить с контролем содержания окиси углерода в отработавших газах. Порядок замера окиси углерода в этом случае будет соответствовать последовательности выполнения работ по определению токсичности отработавших газов.
Правильность регулировки системы холостого хода проверяют изменением режима работы двигателя. При резком открытии дроссельных заслонок двигатель должен плавно и быстро увеличивать частоту вращения коленчатого вала до максимальной. При резком закрытии дроссельных заслонок двигатель должен снижать частоту вращения коленчатого вала до 400-500 об/мин и работать устойчиво.
Электрические контрольно-измерительные приборы газового оборудования - указатель уровня газа в баллоне и манометр первой ступени редуктора проверяют как в комплекте (датчик и указатель), так и раздельно. Раздельную проверку датчика и указателя проводят для определения неисправности одной из сборочных единиц (узлов).
Указанные проверки могут быть выполнены на приборах Э-204-531 и др., которые серийно выпускаются нашей промышленностью и служат для проверки автомобильных контрольно-измерительных приборов.
Установку угла опережения зажигания у двигателей , работающих на газообразном топливе, проводят так же, как и у двигателей, работающих на бензине. Однако регулировка угла опережения зажигания у газовых двигателей газобаллонных автомобилей в связи с высоким октановым числом топлива не может быть проведена по детонации при разгоне автомобиля, поэтому ее проводят при испытаниях автомобиля на стенде с беговыми барабанами по максимальной мощности двигателя.
Проверка герметичности системы питания
Одной из самых ответственных операций, выполняемых при
техническом обслуживании газобаллонных автомобилей, является проверка внешней и
внутренней герметичности системы питания. Наиболее распространенным методом
проверки внешней герметичности системы, находящейся под избыточным давлением,
является обмазывание соединений пенообразующим раствором (водный раствор
хозяйственного мыла или лакричного корня). При отрицательных температурах
добавляется соль - хлористый натрий NaCl или хлористый кальций СаС12.
Таблица 1. Содержание соли в 1 л пенообразующего раствора в зависимости от температуры
Количественное содержание хлористого натрия или кальция в водном растворе зависит от температуры окружающего воздуха, при которой проводят проверку герметичности (табл. 1).
Соединения или участки системы, подлежащие проверке, очищают от грязи и обмазывают с помощью кисти пенообразующим раствором. Проверяемые соединения осматривают дважды - непосредственно при обмазывании данного соединения и после обмазывания. В местах расположения мельчайших не плотностей появляются мелкие пузырьки, скопления которых могут быть обнаружены лишь при повторном осмотре. Во время обмазывания соединений и швов пенообразующим раствором особое внимание обращают на соединения, расположенные в труднодоступных для осмотра местах.
Для определения утечки газа из баллона широко используют электрические газоанализаторы типа ПГФ-2М1-ИЗГ. При пользовании газоанализатором пробу воздуха отбирают из зоны соединения и ручным насосом по шлангу подают в измерительную камеру. После засасывания пробы нажимают кнопку включения питания измерительного моста и снимают показания стрелочного прибора.
При работе с этим прибором следует учитывать, что он не позволяет точно указать место утечки, так как возможно подсасывание газа из других, близко расположенных соединений. Во время проверки автомобиль располагают на открытом воздухе в защищенном от ветра месте.
При обслуживании газобаллонного автомобиля в производственном помещении герметичность газовой системы проверяют сжатым негорючим и нетоксичным газом под давлением 1,6 МПа (воздух, азот или углекислый газ). Сжатые газы используют из баллонов -высокого давления, а сжатый воздух можно подавать от компрессора, обеспечивающего необходимое давление. Проверку проводят при закрытых расходных вентилях газового баллона автомобиля и при отсутствии газа в системе.
При проверке герметичности системы питания от баллона высокого давления (см. Приложение Ё,рис.13.) сжатый инертный газ из баллона 1 подается в редуктор 3, где давление его снижается до 1,6 МПа. Из.редуктора газ через штуцер 6 поступает в систему питания автомобиля. После заполнения системы газом вентиль 4 установки закрывают и проверяют герметичность по образцовому манометру 5.
Падение давления указывает на не герметичность газовой системы автомобиля.
Места утечек определяют пенообразующим раствором. После устранения утечек проверку герметичности повторяют. Газовая система считается герметичной, если падение давления за 15 мин не превышает 0,01-0,15 МПа.
Внутреннюю герметичность проверяют у расходных и
магистрального вентилей. Пропуск газа в систему питания через эти вентили,
когда они находятся в закрытом положении, контролируют по показанию манометра
16 редуктора. Обнаружить утечки газа из расходных вентилей в магистраль можно и
через специальный штуцер на баллоне автомобиля. Для этого отвертывают заглушку
штуцера и обмазывают его пенной эмульсией или берут пробу воздуха прибором
ПГФ-2М1-ИЗГ.
.6 Ремонт ГБО
1.6.1 Виды ремонта
Ремонт -процесс восстановления и поддержания работоспособности автомобиля путем устранения отказов и неисправностей, возникающих в работе или выявленных при техническом обслуживании. Ремонтные работы выполняют по потребности, т. е. после появления отказа или неисправности, или по плану - через определенный пробег или время работы автомобиля (предупредительный ремонт).
Предупредительный ремонт рекомендуется применять для автобусов, автомобилей-такси, автомобилей скорой медицинской помощи, пожарных и других автомобилей, к которым предъявляются повышенные требования безопасности движения и безотказности в работе.
Положением о техническом обслуживании и ремонте автомобиля предусматриваются два вида ремонта: капитальный (КР), производимый на специализированных ремонтных предприятиях, и текущий (ТР), выполняемый в автотранспортных предприятиях или станциях технического обслуживания.
Ремонт включает контрольно-диагностические, разборочные, сборочные, регулировочные, слесарные, медницкие, кузнечные, сварочные, жестяницкие, обойные, электротехнические, шиноремонтные, малярные и другие работы. Ремонт может выполняться по отдельным агрегатам и сборочным единицам (узлам), а также по автомобилю в целом.
Капитальный ремонт предназначен для восстановления работоспособности автомобилей и агрегатов и обеспечения пробега до следующего капитального ремонта (или списания) не менее 80% от нормы для новых автомобилей и агрегатов. Капитальный ремонт агрегата предусматривает его полную разборку, дефектовку (контроль и сортировку деталей по годности), восстановление и замену изношенных деталей, сборку, регулировку, и испытание.
Списание или восстановление агрегата при достижении его базовой (корпусной) деталью предельного состояния осуществляется в соответствии с едиными техническим условиями на сдачу в капитальный ремонт и выдачу из капитального ремонта автомобилей, их агрегатов и сборочных единиц (узлов).
Агрегат направляют в капитальный ремонт, если базовые и основные детали нуждаются в ремонте, требующем полной разборки агрегата; работоспособность агрегата не может быть восстановлена или ее восстановление при текущем ремонте экономически нецелесообразно.
Полнокомплектный автомобиль за срок его службы подвергается, как правило, одному капитальному ремонту, не считая капитального ремонта агрегатов и сборочных единиц(узлов) до и после капитального ремонта автомобиля.
Текущий ремонт предназначен для устранения отказов и неисправностей и способствует выполнению установленных норм пробега до капитального ремонта при минимальных простоях. Он должен обеспечить безотказную работу отремонтированных агрегатов и сборочных единиц (узлов) в течение пробега, не меньшего, чем пробег до очередного ТО-2.
Текущий ремонт выполняют проведением разборочных, слесарных, сварочных и других работ с заменой: у агрегата - отдельных деталей (кроме базовых), достигших предельно допустимого износа, у автомобилей - отдельных агрегатов и сборочных единиц (узлов), требующих текущего или капитального ремонта.
Методы ремонта. Ремонт автомобилей может проводиться индивидуальным или агрегатным методом. При индивидуальном методе снятые агрегаты после их ремонта устанавливают на тот же автомобиль, при этом время простоя автомобиля в ремонте увеличивается на период времени, необходимого для ремонта его агрегатов. Этот метод ремонта применяют при отсутствии оборотного фонда агрегатов, разнотипном составе парка, небольших размерах автотранспортного предприятия и отдаленности его от ремонтного предприятия.
Сущность агрегатного метода ремонта состоит в том, что неисправные или требующие капитального ремонта агрегаты и сборочные единицы (узлы) заменяют исправными.
Агрегатный метод позволяет сократить время простоя автомобиля в ремонте, повысить производительность парка и снизить себестоимость транспортной работы. Поэтому, как правило, текущий ремонт выполняют агрегатным методом.
Восстановление и комплектовка деталей
Ремонт изношенных сопряженных деталей автомобиля можно осуществлять восстановлением начальной посадки изменением размеров деталей или восстановлением размеров деталей до их начального (номинального) значения (Приложение Ё,рис.14.).
При первом способе используют детали ремонтных размеров, больших или меньших номинального. При втором способе на изношенную поверхность детали наносят слой металла, а затем обрабатывают поверхность под номинальный размер. Нанесение слоя металла возможно наплавкой, гальваническими покрытиями и металлизацией расплавленным металлом.
На авторемонтных предприятиях применяют наплавку: под флюсом, в среде защитных газов, вибродуговую и плазменно-дуговую. Из гальванических покрытий наиболее распространены хромирование и отслаивание деталей, а также дуговая металлизация.
К способам нанесения металла на изношенную поверхность относится также заливка подшипников скольжения антифрикционными сплавами (баббитом, свинцовистой бронзой).
Восстановление начальных размеров и посадки некоторых деталей возможно раздачей, осадкой и обжатием.
Для устранения механических, повреждений деталей автомобилей применяют различные виды сварки, пайки, давления, металлизации и слесарной обработки. Коррозионные повреждения устраняют механическим или слесарно-механическим способом (шлифованием, зачисткой и др.). В целях предупреждения коррозии детали оперения, кабину, раму и другие красят, а на детали арматуры кузовов и кабин наносят гальванические покрытия.
Работоспособность и долговечность автомобиля в большой мере зависят от зазоров в сопряжениях. Сборка сопряжений с зазором менее минимально допустимого приводит к нарушению масляной пленки, в результате чего происходит повышенный нагрев трущихся деталей и задиры их рабочих поверхностей.
Сборка с зазорами сверх допустимых приводит к выдавливанию смазки, увеличению динамической нагрузки и износу рабочих поверхностей деталей. Следовательно, зазор между сопряженными деталями выдерживают в полном соответствии с техническими условиями на контроль-сортировку и ремонт деталей.
При ремонте автомобилей в процессе сборки используют детали с номинальными размерами, с ремонтными размерами и с допустимым износом. Поэтому для обеспечения точности сборки необходимо предварительное комплектование, т. е. подбор сопрягаемых деталей по размерам, а некоторых (поршней в двигателе) и по массе. В ряде случаев комплектование сопровождается слесарно-пригоночными операциями, носящими характер частичной сборки.
На крупных авторемонтных предприятиях применяют селективный подбор сопрягаемых деталей. При этом способе комплектования разбивают поле допусков сопрягаемых деталей на несколько равных частей и подбирают детали в пределах одинаковой группы.
Технология ремонта топливной аппаратуры
Совокупность ремонтных операций, выполняемых в определенной последовательности, представляет собой технологию ремонта. В зависимости от объема и условий выполнения ремонта технология может быть различной. Так, капитальный ремонт топливной аппаратуры автомобилей выполняют на специализированных авторемонтных заводах в централизованном порядке. При этом применяется маршрутная технология восстановления приборов, предусматривающая поточный метод производства. Эта технология предполагает высокое оснащение ремонтного процесса современными техническими средствами, которые свойственны крупносерийному производству.
Капитальный ремонт топливной аппаратуры целесообразен в том случае, если затраты на него не превышают себестоимости производства новых приборов. Это условие выполнимо для системы питания дизельных двигателей. Для карбюраторных двигателей, имеющих сравнительно простое конструктивное исполнение приборов системы питания, капитальный ремонт топливной аппаратуры не предусматривается.
В условиях автотранспортного предприятия ремонт топливной аппаратуры выполняют в объеме текущего ремонта. Он включает три этапа: снятие неисправных приборов и деталей с автомобилей на рабочих постах; проверку, восстановление и регулировку приборов в ремонтных цехах или участках; установку на автомобиль снятых и отремонтированных приборов.
Общая схема технологии ремонта топливной аппаратуры автомобилей в автотранспортных предприятиях представлена на рис. 15.
Приемка приборов в ремонт. Перед снятием и отправкой в ремонт неисправные приборы системы питания очищают от грязи, а масло, воду и топливо из внутренних полостей сливают. Приборы снабжают необходимой технической документацией (нарядом на ремонт и др.) и в полном комплекте подготавливают к сдаче в ремонт. Комплектность приборов устанавливают по технической документации и наружным осмотром, затем определяют состояние прибора, оформляя соответствующий акт, где отмечают срок службы до ремонта, состояние базовых деталей и наличие неисправностей.
Рис.15 Схема технологического процесса ремонта топливной аппаратуры
Наружная мойка приборов является обязательной перед разборкой и ремонтом. Ее выполняют различными способами, наиболее простым является мойка с помощью насосных установок.
Для мойки топливной аппаратуры на автомобиле применяют также пароводоструйные очистители. Например, очиститель ОМ-3360 представляет малогабаритную установку для мойки из шланга. Она может работать на пароводяной смеси, холодной или горячей воде, а также на моющих растворах. В качестве моющих растворов рекомендуется применять синтетическое моющее средство «Аэрол». Это сильно пенящееся и нетоксичное средство со специфическим запахом применяется в концентрации 2-3 г/л раствора.
Применение каустической соды в качестве моющего средства следует избегать, так как она опасна для здоровья и вызывает коррозию деталей из цветных металлов.
Качество мойки считается удовлетворительным, если с поверхности приборов системы питания удалены грязь, пыль, отложения и подтеки масла.
Разборка приборов на сборочные единицы (узлы) и детали . Приборы системы питания снимают с двигателя в определенной последовательности. С двигателя вначале снимают топливопроводы высокого и низкого давления и сливные трубопроводы от форсунок и насоса высокого давления. Все топливопроводы укладывают в специальный ящик, чтобы сохранить их конфигурацию. Затем снимают насос высокого давления, вынимая текстолитовую соединительную шайбу с муфты опережения впрыска, и фильтры тонкой и грубой очистки топлива.
Приборы системы питания карбюраторного двигателя снимают примерно в такой же последовательности, начиная с демонтажа подводящих и отводящих топливопроводов и кончая самими приборами.
Снятые с двигателя приборы направляют в цех для ремонта, где их моют в ванне с керосином или в моечной машине, очищают волосяными щетками, продувают сжатым воздухом и разбирают. Для разборки приборов применяют стенды, приспособления и специальный инструмент. После разборки отдельные детали приборов вновь моют в ванне с керосином, очищают от отложений и нагара, продувают сжатым воздухом или вытирают чистыми салфетками, контролируют и сортируют по техническому состоянию.
Контроль и сортировку деталей выполняют с целью определения степени износа и пригодности детали к ремонту или эксплуатации. Детали сортируют на годные к эксплуатации, не подлежащие ремонту и требующие ремонта. Рассортированные детали в зависимости от их состояния отправляют в утиль, на комплектовку или в ремонт.
Комплектовка деталей - это подбор комплекта деталей для одной сборочной единицы (узла) в целом. Например, нагнетательные секции насоса высокого давления можно скомплектовать по паре плунжер - гильза.
Ремонт деталей приборов системы питания сводится к работам по их восстановлению, не требующим сложного оборудования. К ним относятся притирка рабочих поверхностей клапанов и их седел, запорных игл и распылителей форсунок, плунжерных пар, замена потерявших упругость пружин, восстановление целости трубопроводов, резьб, заделка трещин в корпусах, поплавках и др.
При наличии специального оборудования и приспособлений выполняют более сложные ремонтные работы: отслаивание или хромирование изношенных поверхностей кулачков, толкателей, поршней насосов.
Шейки кулачкового вала ремонтируют вибродуговой наплавкой с последующим шлифованием и доведением до необходимого размера.
После ремонта детали приборов системы питания очищают от следов механической обработки, комплектуют по техническим условиям и собирают. Собранные приборы прирабатывают, регулируют и испытывают на стендах, затем устанавливают и регулируют на автомобилях.
газобаллонный оборудование автомобиль ремонт
1.6.2 Ремонт деталей ГБО
Ремонт газового редуктора
Редуктор ремонтируют при возникновении неисправностей, для устранения которых требуется снятие его с автомобиля. К таким неисправностям относятся не герметичность клапана первой ступени, разбухание мембраны, не герметичность вакуумных полостей разгрузочного и экономайзерного устройств, отказ в работе клапана или мембраны второй ступени, срыв резьбы в корпусе редуктора и др. Снятый редуктор моют и в зависимости от характера неисправностей полностью или частично разбирают.
При разборке первой ступени (См. Приложение Д,рис.10.) придерживаются последовательности: ослабляют гайки 13, вывертывают болт 14, пружины высокого давления и вынимают пружину 12, отвертывают гайки и снимают нижнюю крышку 11 редуктора. Разъединив шток мембраны первой ступени с рычажком 5, снимают мембрану 8, вывертывают ось 10 рычажка и вынимают рычажок вместе с клапаном 7. Отвернув две гайки, снимают фильтр 2 вместе с седлом 1 клапана.
При разборке второй ступени редуктора (см. Приложение Д,рис.10.) отвертывают гайки и снимают дозирующе-экономайзерное устройство. Затем извлекают клапан 14. Для этого снимают фланец трубки холостого хода, вывертывают ось 9 рычажка мембраны и снимают рычажок 12 со штока.
Мембрану снимают в такой последовательности: ослабляют стопорный винт и отвертывают колпак 1 седла пружины, вынимают из штока -шплинт 7, снимают упорную шайбу 2 и пружину 3. Затем ослабляют контргайку 4 и вывертывают седло 5 пружины, отвертывают болты, снимают верхнюю крышку 6 редуктора и мембрану 8 в сборе.
Разгрузочное устройство извлекают после разборки второй ступени. Для этого достаточно отвернуть на 2-3 оборота гайку сальника в корпусе редуктора. Разборка разгрузочного
Дозирующе-экономайзерное устройство разбирают в такой последовательности: отвертывают винты и снимают пластину с дозирующими шайбами, снимают крышку, извлекают пружину экономайзера и мембрану, снимают со штока клапана замочную шайбу, вынимают клапан экономайзера и пружину клапана. Снятые детали моют, дефектуют и ремонтируют.
Основными неисправностями корпуса редуктора, которые подлежат устранению, являются повреждение резьбы отверстий и прилегающих плоскостей. Резьбовые отверстия восстанавливают нарезанием резьбы большего размера или постановкой втулок. При ремонте резьбовых отверстий способом увеличения размера резьбы соответственно новому размеру изготовляют шпильки, резьбовые штуцера и т. п.
Повреждения плоскостей прилегания (риски, забоины) устраняют шабрением поверхностей. При обломе ушек под оси рычажков, связывающих клапан и мембрану в первой и второй ступенях, а также при появлении трещин корпус редуктора бракуют.
Не герметичность пары клапан - седло в первой и второй ступенях редуктора устраняют обработкой поверхностей седел и ремонтом клапанов. Повреждения рабочих кромок седел удаляют зачисткой или подрезкой их торца. В клапанах переворачивают или заменяют поврежденные детали вставки. При заедании клапанов зачищают трущиеся поверхности клапанов, а также оси вращения рычажка.
Не герметичность вакуумных полостей разгрузочного и экономайзерного устройств является следствием нарушения целостности или повреждения прилегающих поверхностей. Такие повреждения устраняют шабрением, а поврежденные мембраны заменяют. Мембраны изготовляют по чертежам или образцам из прорезиненной маслобензостойкой ткани толщиной 0,35 мм.
После ремонта редуктор собирают в обратной последовательности. При этом проверяют все подвижные соединения, которые должны перемещаться легко без заеданий. При установке мембран обращают внимание на правильное расположение отверстий для болтов и стержня штока. При прижатии мембран не должно образовываться складок и загибов.
В процессе сборки первой ступени редуктора при необходимости регулируют положение рычажка 5 (см. Приложение Д,рис.10.) винтом 3 и контргайкой 4 до момента, когда плечо рычажка 5 займет горизонтальное положение при полностью закрытом клапане.
После сборки газовый редуктор испытывают на стенде (см. Приложение Ж,рис.16.). Стенд позволяет произвести проверки и регулировки I и II ступеней редуктора, разгрузочного и экономайзерного устройств. Для проведения работ редуктор 1 закрепляют на стенде посредством пневматического приспособления. Проверка работоспособности систем редуктора осуществляется сжатым воздухом с давлением 1,6 МПа и разрежением до 665 Па, создаваемым диафрагменной камерой. Входящее давление воздуха и давление в I ступени редуктора контролируются манометрами 2 и 3. Для замера разрежения во время испытаний используют вакуумметр 4 и пьезометр 5.
В I ступени регулируют величину давления газа, проверяют быстроту наполнения камеры и герметичность соединений. Во II ступени регулируют ход клапана, его герметичность и момент открытия.
Отремонтированные зкономайзерные устройства проверяют на герметичность. При проверке создают разрежение под мембранами не менее 265 Па. Падение вакуума в течение 3 мин не допускается. Кроме того, в экономайзерном устройстве проверяют момент открытия клапана, а в разгрузочном - минимальное разрежение, нейтрализующее усилие конической пружины.
Клапан экономайзера должен открываться при разрежении под мембраной 165+15 Па. Разрежение, нейтрализующее усилие конической пружины разгрузочного устройства, должно составлять 105-135 Па. При несоответствии устройств заданным параметрам пружины тарируют на специальном приборе. Длину пружины замеряют по шкале, нанесенной на стержне. Причем при установке втулки без пружины риска должна совпадать с нулевой отметкой шкалы.
При определении длины пружины в свободном состоянии на
стержень прибора надевают только пружину. При замере длины пружины под
нагрузкой на втулку надевают тарировочный груз. Полученные при замере данные
сравнивают с параметрами пружины (таблица. 2) и в случае несоответствия их
пружину бракуют.
Таблица 2. Параметры пружин экономайзерного и разгрузочного устройств
Ремонт испарителя, фильтра, смесителя и предохранительного клапана
В испарителе газа основными неисправностями, появляющимися в процессе эксплуатации, являются засорение газовых клапанов, не герметичность по плоскости разъема, поры, раковины и трещины в корпусе.
Засорение газовых каналов устраняют при разборке испарителя. Не герметичность по плоскости разъема может возникнуть вследствие повреждения прокладки или плоскости прилегания (заусенцы, забоины и т. п.). При ремонте испарителя прокладку заменяют, а повреждения плоскости разъема исправляют шабрением. Раковины и трещины устраняют заваркой алюминием. Мелкие поры заделывают чеканкой или пропиткой корпусов бакелитовым лаком.
Перед пропиткой газовых каналов бакелитовым лаком испаритель собирают, на выходной штуцер устанавливают заглушку и нагревают его до температуры 80-100°С. Затем через входной штуцер полость заполняют нагретым до такой же температуры бакелитовым лаком и подают воздух под давлением 1,6 МПа.
После непродолжительного времени (около одной минуты) давление снимают, лак из полости выливают и испаритель просушивают до полного высыхания пленки лака. Отремонтированный таким образом испаритель подвергают на стенде (см. Приложение Ж,рис.17.) пневматическим испытаниям на герметичность, конструкция стенда позволяет проверить отдельно в ванне с водой герметичность газовой и водяной полостей испарителя. Подъем и опускание ванны с водой и крепление испарителя осуществляется с помощью пневматической системы.
Проверяют сначала газовую полость под давлением воздуха 1,6 МПа, затем водяную -под давлением воздуха 0,15 МПа. Проверка каждой полости производится в течение 2 мин. Контроль параметров производится по манометрам 2 и 3 и реле времени 4, установленными на панели приборов стенда.
В магистральных газовых фильтрах чаще всего выходит из строя фильтрующий элемент и нарушается герметичность соединений . Для устранения этих неисправностей фильтр снимают и разбирают. При разборке (см. Приложение З,рис.18.) вывертывают болт 1, снимают колпак 2 и вынимают фильтрующий элемент 4. Затем все эти детали промывают и проверяют их техническое состояние. Не герметичность по плоскости разъема фильтра устраняют заменой прокладки или шлифованием плоскостей разъема корпуса и колпака. Фильтрующий элемент при необходимости заменяют. Отремонтированный фильтр проверяют на стенде (см. Приложение З,рис.19.) на герметичность в ванне 4 с водой давлением воздуха в 1,6 МПа в течение 3 мин.
Ремонт смесителя .
В смесителе газа наиболее часто ремонтируют обратный клапан. Для разборки клапана отвертывают винты и открывают крышку клапанной коробки, после чего клапан вместе со стержнем легко вынимается. К неисправностям клапана относится засмоление его или пропуск газа (не герметичность) при работе двигателя на холостом ходу.
Смолистые отложения удаляют промывкой клапана и его стержня в бензине. Не герметичность пары клапан - седло устраняют снятием заусенцев с торцовой поверхности седла и притиркой клапана пастой ГОИ.
После ремонта обратный клапан проверяют на герметичность под давлением воздуха 0,2 МПа и легкость его перемещения. Клапан в любых положениях не должен зависать.
В предохранительном клапане основной неисправностью является не герметичность пары клапан - седло. Не герметичность может быть следствием: попадания грязи (окалины, стружки, песка и т. п.) между седлом и клапаном, повреждения вставки клапана, появления раковин на седле и уменьшения давления пружины на клапан.
Повреждения вставки клапана устраняют зачисткой неровности на прилегающей поверхности бархатным напильником, а раковины на седле -подрезкой или зачисткой его торцовой поверхности. Давление пружины на клапан изменяют набором регулировочных шайб. При увеличении толщины набора шайб давление пружины увеличивается, а при уменьшении - клапан будет открываться при меньшем давлении газа в баллоне. После ремонта, вне зависимости от характера неисправности, предохранительный клапан проверяют и регулируют на давление открытия и закрытия клапана. Проверку можно проводить на грузопоршневом манометре типа МП-60 (см. Приложение И,рис.20.). В один из штуцеров 3 устанавливают проверяемый предохранительный клапан 4, в другой - образцовый манометр 8 на 2 МПа.
Давление в системе прибора создают вспомогательным поршнем и измеряют по образцовому манометру. Кроме того, максимальное давление открытия клапана контролируют основным поршнем. Для этого на его тарелку кладут грузы, соответствующие поднятию поршня при давлении 1,75 МПа. Правильно отрегулированный предохранительный клапан должен открываться при давлении МПа, уменьшить давление в системе и герметично закрыться при давлении 1,45 МПа. После регулировки предохранительный клапан пломбируют.
Освидетельствование баллонов для сжиженного газа
Баллоны для сжиженного газа периодически, один раз в два года, подвергают освидетельствованию. При освидетельствовании проводят гидравлические испытания, определяющие прочность баллонов, и пневматические для проверки герметичности соединений баллонов с арматурой. Перед испытаниями баллоны снимают с автомобиля, освобождают от газа и направляют на предприятие (СТОГА), которое имеет разрешение на проведение указанных работ.
Для механизации трудоемких работ по снятию, постановке и транспортировке газовых баллонов применяют специальную тележку (см. Приложение И,рис.21)
При проведении гидравлических испытаний с баллонов снимают арматуру, на ее место устанавливают заглушки, и баллоны полностью заполняют водой. Испытания проводят под давлением 2,0 МПа, которое создается гидравлическим прессом и измеряется двумя манометрами, один из которых является контрольным.
Под давлением 2,0 МПа баллоны выдерживают в течение 1 мин. Затем давление снижают до рабочего (1,6 МПа), осматривают баллоны снаружи и обстукивают сварные соединения. Баллоны считаются выдержавшими гидравлическое испытание, если не обнаружено признаков разрыва, течи, потения в сварных соединениях на основном металле, видимых остаточных деформаций. После гидравлических испытаний баллоны осушают и на них устанавливают арматуру.
Баллоны в сборе с арматурой подвергают пневматическим испытаниям воздухом или инертным газом под давлением 1,6 МПа. Герметичность соединений определяют при опускании баллона в ванну с водой на 2 мин. Появление пузырьков воздуха на поверхности баллонов и в местах соединений их с арматурой не допускается.
О результатах освидетельствования делают запись в паспорте баллона с указанием выявленных и устраненных неисправностей. На стенке баллона выбивают месяц и год последующих испытаний и ставят клеймо организации, проведшей освидетельствование.
В процессе эксплуатации баллонов при любой замене сборочных единиц (узлов) арматуры проводят внеочередные пневматические испытания без регистрации в паспорте.
Проверка и регулировка газового редуктора и смесителя на моторном стенде.
После ремонта и проверки сжатым воздухом газовый редуктор совместно со смесителем проходят окончательную регулировку и испытания на моторном стенде (см. Приложение Й,рис.22.) при работе двигателя на сжиженном газе.
Моторный стенд оборудован газовым двигателем 1 со всем вспомогательным оборудованием (водяным, масляным и топливным насосами, генератором и т. п.), тормозным 11 и весовым 10 устройствами, позволяющими делать отбор и замерять мощность, развиваемую двигателем.
При испытаниях кроме частоты вращения коленчатого вала и мощности, развиваемой двигателем, замеряют расход топлива газовым счетчиком и давление в различных сборочных единицах (узлах) газового оборудования. Давление газа в баллоне и в первой ступени редуктора замеряют техническими или образцовыми манометрами 5 и 6. Давление и разрежение в газовой аппаратуре, которое должно быть около 0,1 МПа, замеряют ртутным пьезометром. Для измерения малых давлений и разрежений (до 50 Па) используют водяной пьезометр 3.
Во время испытаний проверяют мощностные и экономические показатели двигателя, обеспечиваемые работой редуктора и смесителя.
Первым этапом испытаний является регулировка смесителя и редуктора для работы двигателя на холостом ходу. В смесителе регулируют количество подаваемого газа и воздуха, в редукторе - давление газа во второй ступени на величину 70-80 Па. Одновременно контролируют токсичность отработавших газов и регулируют двигатель.
Следующим этапом испытаний является проверка удельных расходов топлива при работе двигателя с частичной нагрузкой на частоте вращения коленчатого вала 2000 об/мин. Для этого замеряют мощность двигателя и расход газа. Удельный расход в м3(Вт-ч) подсчитывают по формуле , где Vг - расход газа, м3/ч; Nе - действующая мощность двигателя, Вт.
При полном открытии дроссельных заслонок на различной частоте вращения коленчатого вала замеряют мощность двигателя и расход газа.
Кроме того, при моторных испытаниях проверяют работу ограничителя частоты вращения коленчатого вала двигателя.
После, регулировки редуктор и смеситель в комплекте
поступают для установки на автомобиль
1.7 Техническая планировка участка по ремонту ГБО
Приборы систем питания газобаллонных автомобилей, неисправность которых не может быть устранена на постах технического обслуживания и ремонта автомобилей, снимают и направляют в отделение по ремонту газовой аппаратуры и арматуры.
К помещениям отделения предъявляются особые требования. Минимально допустимая высота помещения, обусловленная санитарными нормами, должна быть от пола до потолка 3,2 мм, от пола до выступающих конструктивных элементов перекрытия 2,6 м. Полы должны быть ровными с нескользкой поверхностью, бензомаслоустойчивыми из несгораемого материала. Под помещениями, занятыми отделением, запрещается устраивать подвалы, колодцы и подпольные каналы (пустоты).
Помещение, в котором выполняют обслуживание и ремонт газового оборудования, должно быть оборудовано искусственной приточно-вытяжной вентиляцией с двукратным обменом воздуха, а также противопожарной сигнализацией и средствами пожаротушения.
Снятое с автомобиля газовое оборудование имеет неприятный специфический запах одорирующих веществ, сернистых соединений и остатки пропан-бутанового газа. Поэтому стеллаж-шкаф для хранения газовой аппаратуры в нижней части должен иметь принудительную вытяжную вентиляцию.
Секционный стеллаж-шкаф с переставными полками и
выдвижными ящиками для хранения 20 комплектов газового оборудования представлен
на рис.4. Стеллаж имеет принудительный отсос воздуха производительностью 0,25
м3/ч. Для предохранения газовой аппаратуры от повреждений секции стеллажа
выполнены из материала меньшей твердости (дерево, пластмасса), чем агрегат
аппаратуры.
Рис. 23. Стеллаж-шкаф для хранения газового оборудования
При мойке газового оборудования применяют те же машины и средства, что и для деталей бензиновой и дизельной топливной аппаратуры. Газовые приборы размещают на верстаках, оборудованных тисками и устройством бортового отсоса воздуха.
На участке технического обслуживания и ремонта осуществляют дефектовку, сборку, проверку и регулировки деталей и сборочных единиц (узлов) газового оборудования.
Монтажно-демонтажные, слесарные и регулировочные работы по газовому оборудованию выполняют с помощью специального инструмента. Для этих целей применяют комплект инструмента модели И-139 , который имеет медное покрытие, позволяющее применять его во взрывоопасной среде. Проверку и регулировку выполняют на специальных испытательных стендах. Определяют рабочие параметры газового оборудования и проверяют внутреннюю и внешнюю герметичность.
Для проверки и регулировки газового смесителя и карбюратора-смесителя участок оборудуют безмоторной установкой. Вакуумная часть этой установки размещена в отдельном помещении.
Рабочие параметры и герметичность сборочных единиц
(узлов) газового оборудования проверяют сжатым воздухом или инертным газом при
рабочем давлении 1,6 МПа. Сжатый газ подается из баллонов высокого давления (до
20 МПа) и редуцируется до испытательного давления. Шкаф для хранения этих баллонов
и тележка для их перемещения размещены на участке энергообеспечения.
1.8 Техника безопасности при ТО и ремонте ГБО
Сжиженные нефтяные и сжатые природные газы обладают повышенными по сравнению с жидкими моторными топливами пожаро- и взрывоопасными свойствами, которые могут проявляться при утечке газа из топливной системы автомобиля, находящейся под давлением.
Нефтяные газы не обладают токсичным (отравляющим) воздействием на человеческий организм, но наличие их в воздухе уменьшает содержание кислорода. Человек, находящийся в такой атмосфере, будет испытывать кислородное голодание. Предельно допустимая концентрация паров пропана в рабочей зоне, установленная санитарными нормами, составляет 1800 мг/м3. Пары нефтяного газа в 1,5-2 раза тяжелее воздуха и скапливаются в низких и непроветриваемых местах, образуя взрывоопасную концентрацию. При работе со сжиженным газом следует иметь в виду, что, вытекая из баллона, он быстро испаряется с интенсивным поглощением теплоты. Попадание сжиженного газа на незащищенную поверхность тела человека вызывает обморожение, которое по характеру воздействия напоминает ожог.
Природный газ в 1,5-1,8 раза легче воздуха, поэтому при утечках он скапливается вверху, создавая в помещении пожаро- и взрывоопасную ситуацию. Его содержание в рабочей зоне не должно превышать 300 мг/м3. По степени воздействия на человека природный газ относится к 4-му классу малоопасных веществ.
Перед постановкой автомобиля в профилакторий на техническое обслуживание и ремонт закрывают вентили на баллоне, вырабатывают весь газ, находящийся в системе питания, и проверяют герметичность газового баллона. Если на автомобиле, находящемся в помещении, обнаружена утечка газа, его буксируют на улицу, а помещение проветривают с целью удаления газовоздушной смеси, особенно из осмотровых канав.
При обслуживании и ремонте газобаллонного автомобиля категорически запрещается: ремонтировать газовую аппаратуру, находящуюся под давлением, и арматуру баллона, если в баллоне имеется газ; пускать двигатель при наличии в системе питания утечек газа; пускать двигатель и работать на смеси двух топлив (бензина и газа); счищать краску и красить наполненный газом баллон; открывать и закрывать вентили баллона с помощью дополнительных рычагов. Все работы по снятию, установке и регулированию газового оборудования следует выполнять специальным инструментом с медным покрытием.
В помещениях технического обслуживания и ремонта во время нахождения в них газобаллонных автомобилей нельзя пользоваться открытым огнем, выполнять сварочные работы, работать на заточных станках, кузнечных горнах и другом оборудовании, вызывающем искрообразование.
У газобаллонных автомобилей запрещается проверять пламенем герметичность соединений газовой аппаратуры и газопроводов и подносить к автомобилю открытый огонь для освещения, пайки, сварки и т. п.
В случае возникновения пожара на автомобиле следует немедленно закрыть магистральный и расходные вентили. Если пожар возник при работающем двигателе, то необходимо при закрытых газовых вентилях увеличить число оборотов коленчатого вала, с тем чтобы быстрее израсходовать газ из системы питания. Вспыхнувший газ можно тушить углекислотным огнетушителем, песком и кошмой. Вода при тушении пожара может быть применена для охлаждения баллона с целью предупреждения чрезмерного повышения в нем давления.
Общим требованием при эксплуатации газобаллонных
автомобилей, работающих на сжиженном и сжатом газах, является обучение и сдача
экзаменов персоналом, производящим эксплуатацию, техническое обслуживание и
ремонт этих автомобилей.
1.9 Охрана труда на предприятии
К самостоятельной работе слесарем по ремонту автомобилей (далее - слесарем) допускаются лица не моложе 18 лет, имеющие профессиональную подготовку и прошедшие:
предварительный медицинский осмотр. При уклонении от прохождения медицинских осмотров работник не допускается к выполнению трудовых обязанностей;
вводный инструктаж;
обучение безопасным методам и приемам труда и проверку знания безопасности труда;
первичный инструктаж на рабочем месте.
К работе с электрифицированными инструментом и оборудованием допускаются слесари, прошедшие соответствующее обучение и инструктаж, имеющие I квалификационную группу по электробезопасности.
Выполнение работ, не связанных с обязанностями слесаря, допускается после проведения целевого инструктажа.
Слесарь обязан:
Соблюдать нормы, правила и инструкции по охране труда, пожарной безопасности и правила внутреннего трудового распорядка.
Правильно применять коллективные и индивидуальные средства защиты, бережно относиться к выданным в пользование спецодежде, спец. обуви и другим средствам индивидуальной защиты.
Немедленно сообщать своему непосредственному руководителю о любом несчастном случае, происшедшем на производстве, о признаках профессионального заболевания, а также о ситуации, которая создает угрозу жизни и здоровью людей.
Выполнять только порученную работу. Выполнение работ повышенной опасности производится по наряду-допуску после прохождения целевого инструктажа.
Запрещается употреблять спиртные напитки, а также приступать к работе в состоянии алкогольного или наркотического опьянения. Курить разрешается только в специально оборудованных местах.
Опасными и вредными производственными факторами для слесаря при ремонте автомобилей являются: токсичные, горючие жидкости, смазочные материалы и их испарения;
выхлопные газы двигателя;
электрический ток;
Движущиеся части узлов и агрегатов;
острые кромки деталей, узлов, агрегатов, инструмента и приспособлений.
Спецодежда и другие средства индивидуальной защиты выдаются согласно Типовым отраслевым нормам.
Работодатель обязан заменить или отремонтировать спецодежду, спец. обувь и другие средства индивидуальной защиты, пришедшие в негодность до истечения установленного срока носки по причинам, не зависящим от работника.
При заболевании или травмировании как на работе, так и вне ее необходимо сообщить об этом руководителю и обратиться в лечебное заведение.
При несчастном случае следует оказать помощь пострадавшему в соответствии с инструкцией по оказанию доврачебной помощи, вызвать работника медицинской службы. Сохранить до расследования обстановку на рабочем месте такой, какой она была в момент происшествия, если это не угрожает жизни и здоровью окружающих и не приведет к аварии.
При обнаружении неисправности оборудования, приспособлений, инструмента сообщить об этом руководителю. Пользоваться и применять в работе неисправные оборудование и инструменты запрещается.
Выполняя трудовые обязанности, слесарь обязан соблюдать следующие требования:
ходить только по установленным проходам, переходным мостикам и площадкам;
не садиться и не облокачиваться на случайные предметы и ограждения;
не подниматься и не спускаться бегом по лестничным маршам и переходным мостикам;
не прикасаться к электрическим проводам, кабелям электротехнических установок;
не устранять неисправности в осветительной и силовой сети, а также пусковых устройствах;
не находиться в зоне действия грузоподъемных машин.
Обращать внимание на знаки безопасности, сигналы и выполнять их требования. Запрещающий знак безопасности с поясняющей надписью "Не включать - работают люди!" имеет право снять только тот работник, который его установил. Запрещается включать в работу оборудование, если на пульте управления установлен запрещающий знак безопасности с поясняющей надписью "Не включать - работают люди!"
При передвижении по территории необходимо соблюдать следующие требования:
ходить по пешеходным дорожкам, тротуарам;
переходить железнодорожные пути и автомобильные дороги в установленных местах;
при выходе из здания убедиться в отсутствии движущегося транспорта.
Для питья следует употреблять воду из сатураторов, оборудованных фонтанчиков или питьевых бачков.
Принимать пищу следует в оборудованных помещениях (столовой, буфете, комнате приема пищи).
Выполнение работ повышенной опасности производится по наряду-допуску после прохождения целевого инструктажа.
Требования безопасности перед началом работы
Надеть спецодежду. Убедиться, что она исправна. Работать в легкой обуви (тапочках, сандалиях, кроссовках, кедах) не разрешается.
Автомобили, направляемые на посты технического обслуживания и ремонта, должны быть вымыты, очищены от грязи и снега. Постановка автомобилей на посты технического обслуживания и ремонта осуществляется под руководством ответственного лица.
После постановки автомобиля на пост необходимо затормозить его стояночным тормозом, выключить зажигание (перекрыть подачу топлива в автомобиле с дизельным двигателем), установить рычаг переключения передач в нейтральное, положение, под колеса подложить не менее двух специальных упоров (башмаков). На рулевое колесо должна быть повешена табличка с надписью "Двигатель не пускать - работают люди!" На автомобилях, имеющих дублирующее устройство для пуска двигателя, аналогичная табличка должна вывешиваться и у этого устройства.
При обслуживании автомобиля на подъемнике на пульте управления подъемником должна быть вывешена табличка с надписью "Не трогать - под автомобилем работают люди!"
В рабочем (поднятом) положении плунжер гидравлического подъемника должен надежно фиксироваться упором (штангой), гарантирующим невозможность самопроизвольного опускания подъемника.
Перед проведением работ, связанных с проворачиванием коленчатого и катанного валов, необходимо дополнительно проверить выключение зажигания (перекрытие подачи топлива для дизельных автомобилей), нейтральное положение рычага переключения передач, освободить рычаг стояночного тормоза.
После выполнения необходимых работ автомобиль следует затормозить стояночным тормозом.
При необходимости выполнения работ под автомобилем, находящимся вне осмотровой канавы, подъемника, эстакады, работники должны обеспечиваться лежаками.
Подмости должны быть устойчивыми и иметь поручни и лестницу. Металлические опоры подмостей должны быть надежно связаны между собой.
Доски настила подмостей должны быть уложены без зазоров и надежно закреплены. Концы досок должны находиться на опорах. Толщина досок подмостей должна быть не менее 40 мм.
Переносные деревянные лестницы-стремянки должны иметь врезные ступеньки шириной не менее 150 мм.
Лестница-стремянка должна быть такой длины, чтобы рабочий мог работать со ступеньки, отстоящей от верхнего конца лестницы не менее чем на 1 м. Нижние концы лестницы должны иметь наконечники, препятствующие ее скольжению.
Перед снятием узлов и агрегатов системы питания, охлаждения и смазки автомобиля, когда возможно вытекание жидкости, необходимо предварительно слить из них топливо, масло и охлаждающую жидкость в специальную тару, не допуская их проливания.
Перед началом работы с электроинструментом следует проверить наличие и исправность заземления. При работе электроинструментом с напряжением выше 42 В необходимо пользоваться защитными средствами (резиновыми перчатками, галошами, ковриками, деревянными сухими стеллажами).
Перед тем, как пользоваться переносным светильником, необходимо проверить, есть ли на лампе защитная сетка, исправны ли кабель и его изоляция.
Осмотровые канавы, траншеи и тоннели должны содержаться в чистоте, не загромождаться деталями и различными предметами. На полу канавы должны устанавливаться прочные деревянные решетки. Осмотровые канавы и эстакады должны иметь колесоотбойные брусья (реборды).
Автомобили, работающие на газовом топливе, могут въезжать на посты технического обслуживания и ремонта только после перевода их на работу на бензин (дизельное топливо).
Расходные вентили не следует оставлять в промежуточном состоянии: они должны быть или полностью открыты, или полностью закрыты.
Перед въездом необходимо проверить на специальном посту газовую систему питания на герметичность. Въезжать в помещения с негерметичной газовой системой питания запрещается.
Газ из баллонов автомобиля, на котором должны проводиться сварочные, окрасочные работы, а также работы, связанные с устранением неисправностей газовой системы питания или ее снятием, должен быть предварительно полностью слит (выпущен) на специально отведенном месте (посту), а баллоны продуты сжатым воздухом, азотом или другим инертным газом.
Перед сдачей автомобилей, работающих на газовом топливе, в капитальный ремонт газ из баллонов должен быть полностью выработан (выпущен, слит), а сами баллоны продегазированы. При необходимости баллоны вместе с газовой аппаратурой могут быть сняты и сданы для хранения на склад.
Требования безопасности во время выполнения работы
При выполнении операций по техническому обслуживанию, требующему работы двигателя автомобиля, выхлопную трубу соедините с вытяжной вентиляцией, а при ее отсутствии примите меры по удалению из помещения отработанных газов.
При вывешивании части автомобиля, прицепа, полуприцепа подъемными механизмами (домкратами, талями и т. п.), кроме стационарных, необходимо вначале подставить под неподнимаемые колеса специальные упоры (башмаки), затем вывесить автомобиль, подставить под вывешенную часть козелки и опустить на них автомобиль.
Запрещается :
работать лежа на полу (земле) без лежака;
выполнять какие-либо работы на автомобиле (прицепе, полуприцепе), вывешенном только на одних подъемных механизмах (домкратах, талях и т.п.), кроме стационарных;
подкладывать под вывешенный автомобиль (прицеп, полуприцеп) вместо козелков диски колес, кирпичи и другие случайные предметы;
снимать и ставить рессоры на автомобилях (прицепах, полуприцепах) всех конструкций и типов без предварительной их разгрузки от массы кузова путем вывешивания кузова с установкой козелков под чего или раму автомобиля.
проводить техническое обслуживание и ремонт автомобиля при работающем двигателе, за исключением отдельных видов работ, технология проведения которых требует пуска двигателя;
поднимать (вывешивать) автомобиль за буксирные приспособления (крюки) путем захвата за них тросами, цепью или крюком подъемного механизма;
поднимать (даже кратковременно) грузы массой более, чем это указано на табличке данного подъемного механизма,
снимать устанавливать и транспортировать агрегаты при зачаливании их тросом или канатами;
поднимать груз при косом натяжении троса или цепей;
работать на неисправном оборудовании, а также с неисправными инструментами и приспособлениями;
оставлять инструмент и детали на краях осмотровой канавы;
работать под поднятым кузовом автомобиля-самосвала, самосвального прицепа без специального дополнительного упора;
использовать случайные подставки и подкладки вместо специального дополнительного упора;
работать с поврежденными или неправильно установленными упорами;
пускать двигатель и перемещать автомобиль при поднятом кузове;
производить ремонтные работы под поднятым кузовом автомобиля-самосвала, самосвального прицепа без предварительного его освобождения от груза;
проворачивать карданный вал при помощи лома или монтажной лопатки;
сдувать пыль, опилки, стружку, мелкие обрезки сжатым воздухом:
Ремонт, замена подъемного механизма кузова автомобиля-самосвала, самосвального прицепа или долива в него масла должны производиться после установки под поднятый кузов специального дополнительного упора, исключающего возможность падения или самопроизвольного опускания кузова.
При ремонте и обслуживании автобусов к грузовых автомобилей рабочие должны бить обеспечены подмостями или лестницами стремянками. Применять приставные лестницы не разрешается.
В зоне технического обслуживания и ремонта автомобилей запрещается:
протирать автомобиль, и мыть агрегаты легковоспламеняющимися жидкостями (бензином, растворителями и т. п.);
хранить легковоспламеняющиеся жидкости и горючие материалы, кислоты, краски, карбид кальция и т. д. в количествах больше сменной потребности;
заправлять автомобиль топливом;
хранить чистые обтирочные материалы вместе с использованными;
загромождать проходы между стеллажами и выходы из помещений материалами, оборудованием, тарой, снятыми агрегатами и т. п.;
хранить отработанное масло, порожнюю тару из-под топлива и смазочных материалов.
При проведении работ по техническому обслуживанию и ремонту автомобилей на газовом топливе необходимо:
Поднять капот для проветривания;
выполнять работы по снятию, установке и ремонту газовой аппаратуры только с помощью специальных приспособлений, инструмента и оборудования; агрегаты газовой аппаратуры разрешается снимать только в остывшем состоянии (при температуре поверхности деталей не выше +60 °С);
проверять герметичность газовой системы питания сжатым воздухом, азотом или иными инертными газами при закрытых расходных и открытом магистральном вентилях;
предохранять газовое оборудование от загрязнения и механических повреждений;
крепить шланги на штуцерах хомутиками.
Регулировку приборов газовой системы питания непосредственно на автомобиле следует производить в отдельном специально оборудованном помещении, изолированном от других помещений перегородками (стенами).
При проведении технического обслуживания и ремонта автомобилей, работающих на газовом топливе, запрещается:
Подтягивать резьбовые соединения и снимать с автомобиля детали газовой аппаратуры и газопроводы, находящиеся под давлением;
выпускать сжатый газ в атмосферу или сливать сжиженный газ на землю;
скручивать, сплющивать и перегибать шланги и трубки, использовать замасленные шланги;
устанавливать газопроводы кустарного производства;
применять дополнительные рычаги при открывании и закрывании магистрального и расходных вентилей;
использовать для крепления шлангов проволоку или иные предметы.
При работе гаечными ключами необходимо подбирать их соответственно размерам гаек, правильно накладывать ключ на гайку. Нельзя поджимать гайку рывком.
При работе зубилом или другим рубящим инструментом необходимо пользоваться защитными очками для предохранения глаз от поражения металлическими частицами, а также надевать на зубило защитную шайбу для защиты рук.
Проверять соосность отверстий разрешается при помощи конусной оправки, а не пальцем.
Снятые с автомобиля узлы и агрегаты следует устанавливать на специальные устойчивые подставки, а длинные детали - на стеллажи.
При работе пневматическим инструментом подавать воздух разрешается после установки инструмента в рабочее положение.
Соединять шланги пневматического инструмента и разъединять их разрешается после отключения подачи воздуха.
Паяльные лампы, электрические и пневматические инструменты разрешается выдавать лицам, прошедшим инструктаж и знающим правила обращения с ними.
При проверке уровня масла и жидкости в агрегатах запрещается пользоваться открытым огнем.
При замене или доливе масел и жидкостей в агрегаты сливные и заливные пробки необходимо откручивать и закручивать предназначенным для этой цели инструментом.
Для подачи смазки в высоко расположенные масленки необходимо пользоваться стандартной подставкой под ноги в осмотровой канаве.
Для работы впереди и сзади автомобиля и для перехода через осмотровую канаву необходимо пользоваться переходными мостиками, а для спуска в осмотровую канаву и подъема из нее - специальными лестницами.
Запрещается:
Подключать электроинструмент к сети при отсутствии или неисправности штепсельного разъема;
переносить электрический инструмент, держа его за кабель, а также касаться рукой вращающихся частей до их остановки;
направлять струю воздуха на себя или на других при работе пневматическим инструментом;
устанавливать прокладку между зевом ключа и гранями гаек и болтов, а также наращивать ключ трубой или другими рычагами, если это не предусмотрено конструкцией ключа.
Для испытания и опробования тормозов на стенде необходимо принять меры, исключающие самопроизвольное скатывание автомобиля с валиков стенда.
Работа на диагностических и других постах с работающим двигателем разрешается при включенной местной вытяжной вентиляции, эффективно удаляющей отработанные газы.
Запрещается работать в производственных помещениях, где выделяются вредные вещества, неисправна либо не выключена вентиляция.
На участках и в цехах, где ведутся работы с деталями, загрязненными этилированным бензином, должны устанавливаться бачки с керосином.
В случае попадания этилированного бензина на кожу рук или другие части тела необходимо обмыть эти места керосином, а затем теплой водой с мылом.
Запрещается работать на оборудовании со снятым, незакрепленным или неисправным ограждением.
Работы под поднятыми кузовами машин проводятся при установленной упорной штанге, предотвращающей опускание кузова.
Снятие и установку пружин производят специальными съемниками.
Выпрессовку и запрессовку втулок, подшипников и других деталей с плотной посадкой производят с помощью специальных приспособлений, прессов или молотков с медными бойками.
При ремонте автомобилей с высоким расположением узлов и деталей применяются лестницы-стремянки со ступенями шириной не менее 150 мм. Применять приставные лестницы запрещается.
Перед началом работ, связанных с проворачиванием коленчатого или карданного валов, выключить зажигание, перекрыть подачу топлива
При работе под автомобилем пользуйтесь защитными очками, лежаками.
Замену рессор производите после их разгрузки и установки автомобиля на подставки.
При запуске двигателя держать заводную рукоятку так, чтобы все пальцы руки обхватывали ее с одной стороны.
При обкатке двигателя остерегайтесь его вращающихся частей.
Перед накачиванием шин после их установки на колесо убедитесь, что запорное кольцо правильно установлено в пазе диска.
Во избежание травм вылетающим диском накачивать колесо следует с предохранительной вилкой или в специальной клети.
Нельзя снимать с машины агрегаты, узлы, в то время, когда под машиной работают люди.
Нельзя укладывать и ставить около машины, на подножки, на эстакады снятые агрегаты, узлы и детали, так как они могут упасть и нанести травму работающим.
При замене мостов и рессор под поднятый конец рамы подставьте специальные подставки. Запрещается вместо подставок использовать различные предметы или оставлять машину на домкратах.
Требования безопасности по окончании работы
Приведите в порядок рабочее место. Уберите инструменты и приспособления.
Убирать рабочее место от пыли, опилок, стружки, мелких металлических обрезков следует щеткой.
Доложите руководителю о возникавших в процессе работы неисправностях.
Очистите спецодежду, спец обувь и другие средства индивидуальной защиты.
Вымойте лицо и руки мылом или примите душ.
Требования безопасности в аварийных ситуациях
В случае отключения электропитания прекратите работу и доложите руководителю. Не пытайтесь самостоятельно выяснять и устранять причину. Помните, что напряжение может неожиданно появиться.
При возникновении пожара сообщить в пожарную охрану по телефону (указать номер телефона), руководителю работ и приступить к тушению.
При загорании или пожаре помните, что тушить электроустановки следует углекислотными огнетушителями, сухим песком во избежание поражения электрическим током.
Разлитое масло и топливо необходимо немедленно удалять с помощью леска или опилок, которые после использования следует ссыпать в металлические ящики с крышками, устанавливаемые вне помещения.
При любой неисправности редукторов высокого и низкого
давления, электромагнитного запорного клапана необходимо закрыть расходные и
магистральный вентили, а неисправные узлы снять с автомобиля и направить на
проверку в специальную мастерскую (на специализированный участок).
Заключение
Автомобильный транспорт является основным потребителем
жидких топлив - бензина и дизельного топлива, при сгорании которых выделяются
вредные для человека и окружающей среды вещества - отработавшие газы.
Постоянный рост числа автомобилей приводит как к неуклонному сокращению запасов
сырья для производства топлив - нефти, так и к накоплению в окружающей среде
вредных веществ, поступающих с отработавшими газами. Расширить сырьевую базу
автомобильных топлив и одно- временно уменьшить вредное воздействие на экологию
можно за счет использования так называемых нетрадиционных, или альтернативных,
топлив. Наибольшее распространение на автомобильном транспорте получили газообразные
углеводородные топлива, которые относятся к чистым в экологическом отношении
моторным топливам. Стоимость газообразного топлива в два три раза ниже
стоимости бензина и дизельного топлива, а запасы его сырья превосходят
нефтяные. Эти факторы обусловили применение газа на автотранспорте. Во многих
странах на государственном уровне приняты экологические программы и законы по
снижению вредного влияния отработавших газов автомобильного транспорта за счет
использования газового топлива. Наибольших успехов в решении этих задач наряду
с Россией достигли Италия, Австралия, Аргентина, Австрия, Швеция, Канада, Новая
Зеландия, США и Япония.
Литература
1. Напольский Г.М. Технологическое проектирование автотранспортных предприятий и станций технического обслуживания: Учебник для ВУЗов.-2-е изд., перераб. и доп.- М: Транспорт, 1993.-271с.
Положение о техническом обслуживании и ремонте подвижного состава авто мобильного транспорта -М: Транспорт, 1988.-78с.
С.Афонин. Газовое оборудование автомобиля. Легковые, грузовые. Устройство, установка, обслуживание. Практическое руководство. «ПОНЧиК», 2001 г.
Буралев Ю.В. и др. Устройство, обслуживание и ремонт топливной аппаратуры автомобилей. - М.: Высшая школа, 1982 г.
5. Автослесарь. Устройство, техническое обслуживание и ремонт автомобилей: Учебное пособие / Под ред. А.С. Трофименко. Ростов н/Д: Феникс, 2001
Руководство по эксплуатации, техническому обслуживанию и ремонту автомобилей ВАЗ 2106.Сост. В.А. Яметов, А.П. Игнатов. - М.: Издательство «РусьАвтокнига», 2003.
8. Техническое обслуживание и ремонт
автомобилей: Учебник для студ. Учреждений сред. Проф. Образования / В.М.
Власов, С.В. Жанказиев. - М.: Издательский центр «Академия», 2003
Приложения
Приложение А
Рис.1. Газовый баллон
Рис.2. Блок запорно-контрольной и предохранительной арматуры:
предохранительный клапан; 2 шарик; 3 заправочный вентиль; 4 скоростной
клапан; 5 - прокладка; 6 - прозрачная крышка; 7 - контрольная стрелка; 8 -
шкала; 9 - автоматический клапан; 10 - трубка забора газа; 11 -поплавок; 12 -
регулировочный винт; 13 - расходный вентиль
Приложение Б
Рис.3 Выносное заправочное устройство:
Пробка; 2 - прокладка резиновая; 3 - корпус; 4 - седло клапана; 5 -
клапан; 6 - пружина; 7 - кронштейн; 8 - гайка; 9 - кольцо уплотнительное; 10 -
штуцер выходной
Рис.6.Электромагнитные газовые клапаны. Внешний вид
Приложение В
Рис.7. Cхема электромагнитного газового
клапана: 1 - направляющая втулка;2, 6 - стопорное кольцо; 3 пружина; 4 - якорь;
5 - катушка; 7 - уплотнитель; 8 - корпус; 9 - входной канал; 10 - металлическая
обойма с фильтром; 11 - резиновое кольцо; 12 - отстойник; 13 - выходной канал;
14 - постоянный кольцевой магнит; 15 - кольцевая полость; 16 - уплотнитель
Рис.8. Электромагнитные бензиновые клапаны: а - с ручкой; б - с нижним
вентилем; в - с боковым вентилем
Приложение Г
Рис.9.Схема электромагнитного бензинового клапана:
Входная полость; 2, 20 - штуцер; 3, 8 - уплотнительные прокладки; 4 -
фильтр; 5 - корпус; 6 - выходная полость; 7 - винт крепления; 9 - центрирующий
толкатель; 10 - корпус электромагнита; 11 - пружина; 12 - катушка
электромагнита; 13 - запорная шайба; 14 - вывод обмотки катушки электромагнита;
15 - выходной штуцер; 16 - уплотнитель; 17 - газовый штуцер; 18 - кронштейн
крепления; 19 - гайка
Приложение Д
Рис.10. Первая ступень редуктора в сборе и ее детали в разобранном виде:
1 - седло клапана,2 - фильтр,3 - регулировочный винт;4,13 - контргайки,5 -рычажок,6 - шток,7 - клапан в сборе,8 - мембрана в сборе,9 - прокладка,10 - ось рычажка, 11 - крышка, 12 - пружина,14 - седло пружины (регулировочный болт)
Детали второй ступени редуктора:
Колпак, 2 -шайба, 3 - пружина, 4, 11 - контргайки, 5 - седло пружины 6 - крышка, 7 - шплинт, 8 - мембрана в сборе, 9 - ось рычажка, 10 - прокладка, 12 - рычажок, 13 - регулировочный винт, 14 - клапан, 15 - вставка клапана, 16 - седло клапана
Приложение Е
Рис.11. Приспособление для замера хода клапана второй ступени редуктора:
Седло, 2 - клапан, 3 - крышка люка, 4, 8 - контргайки, 5 - регулировочный винт, 6 - рычаг. 7 - мембрана второй ступени, 9 - регулировочный стакан, /0 - пружина, 11 - шток, 12 - стопорный винт, 13 - линейка, 14 - движок линейки
Рис.12.Инструмент для регулировки клапана второй ступени редуктора: 1 - отвертка, 2 - специальный торцовый ключ
Приложение Ё
Рис.13.Схема установки для проверки герметичности системы питания газобаллонного автомобиля:
Баллон со сжатым инертным газом. 2 - вентиль баллона, 3 - редуктор, 4 - вентиль установки, 5 - образцовый манометр, 6 - штуцер, 7 - баллон для сжиженного газа
Рис.14.Способы восстановления деталей
Приложение Ж
Рис.16.Стенд для испытания газового редуктора:
Газовый редуктор, 2-манометр высокого давления, 3 - манометр низкого давления, 4 - вакуумметр, 5 - пьезометр.6 - вентили управления
Рис.17.Стенд для испытания испарителя:
Рычаги управления, 2 - манометр для испытания газовой полости, 3 - манометр для испытания водяной полости, 4 - реле времени
Приложение З
Рис.18.Магистральный фильтр газа:
Болт, 2 - колпак, 3 - прокладка, 4 - фильтрующий элемент, 5 - корпус, 6 - штуцер, 7 - электромагнитный клапан
Рис.19.Стенд для испытания фильтров: 1 - баллон со сжатым воздухом, 2 - манометры, 3 - рычаг управления, 4 - ванна с водой
Приложение И
Рис.20.Схема грузопоршневого манометра МП-60: 1 - корпус, 2 - вспомогательный поршень, 3 - штуцер, 4 - предохранительный клапан, 5 - колонка, 6 - основной поршень, 7 - тарировочные грузы, 8 - образцовый манометр
Рис.21.Тележка для снятия и постановки газовых баллонов:
Рама. 2 - газовый баллон. 3 - стрела с пантографом, 4 - стойка. 5 - ножной насос
Приложение Й
Рис.22.Схема моторного стенда:
Двигатель, 2 - счетчик для замера расхода газа, 3 - водяной пьезометр, 4 - ртутный пьезометр, 5 - манометр редуктора, 6 - манометр баллона, 7 -указатель уровня газа вбаллоне, 8 - газовый баллон, 9 - бак с бензином, 10 - весовое устройство, 11 - тормозное устройство, 12 - прибор для замера токсичности отработавших часов
Система питания двигателя от газобаллонной установки
Двигатели газобаллонных автомобилей работают на газообразном топливе, запас которого находится в баллонах, установленных на автомобилях.
Применение газобаллонных автомобилей дает возможность использовать имеющиеся в нашей стране значительные ресурсы дешевых горючих газов. Мощность двигателя и грузоподъемность газобаллонных автомобилей такие же, как у базовых автомобилей с карбюраторными двигателями. Поэтому эксплуатация газобаллонных автомобилей технически и экономически целесообразна.
Топливо для газобаллонных автомобилей. В качестве топлива для их двигателей используют смеси сжиженных (точнее, легкосжижае-мых) газов, получаемых из попутного нефтяного и природного газов.
Для газобаллонных автомобилей промышленность выпускает смеси пропана и бутана технических (СПБТ) двух составов:
СПБТЗ - зимнюю, содержащую не менее 75% пропана и не более 20% бутана;
СПБТЛ - летнюю, содержащую не менее 34% пропана и не более 60% бутана.
Помимо пропана и бутана, в состав топлива входят также метан, этан, этилен, пропилен, бутилен, пентан и другие, общее содержание которых в смеси составляет 5…6%.
Пропановые фракции (пропан и пропилен) обеспечивают необходимое давление в газовом баллоне автомобиля. Бутановая составляющая (нормальный бутан, изобутан, бутилен, изобутилен) - наиболее калорийный и легкосжижаемый компонент сжиженных газов.
Важнейшими свойствами сжиженных газов, определяющими их пригодность для использования в качестве топлива для газобаллонных автомобилей, являются: теплота сгорания пропана - 45,7 (10972), бутана - 45,2 (10845), бензина - 43,8 (10500) МДж/кг (ккал/кг); плотность жидкого пропана - 0,509, а бутана - 0,582 кг/м3; октановое число у пропана - 120, у бутана - 93.
Газ не должен содержать механических примесей, водорастворимых кислот, щелочей, смол и других вредных примесей.
Давление насыщенных паров для смеси сжиженных газов колеблется в пределах от 0,27 МПа (2,7 кгс/см2) при температуре - 20 °С до 1,6 МПа (16 кгс/см2) при температуре +45 °С.
Сжиженные газы обладают большим коэффициентом объемного расширения. Поэтому баллоны следует заполнять газом не более чем на 90% их объема. Остальные 10% составляет объем паровой подушки, без которой даже незначительное повышение температуры газа приводит к резкому увеличению давления в баллоне (примерно 0,7 МПа, или 7 кгс/см2 на ГС повышения температуры сжиженного газа).
Газобаллонная установка. Отечественная автомобильная промышленность выпускает газобаллонные грузовые автомобили ЗИЛ-138, ГАЗ-53-07 и автобусы ЛАЗ-695П и ЛИАЗ-677Г. Все эти автомобили отличаются от базовых моделей ЗИЛ-130, ГАЗ-53А, ЛАЗ-695Н и ЛИАЗ-677 наличием газобаллонной установки, а также модифицированным газовым двигателем, имеющим более высокую, чем базовый карбюраторный двигатель, степень сжатия.
Для обеспечения возможности передвижения автомобиля при неисправности газобаллонной установки или отсутствии газа в системе питания имеется карбюратор, на котором двигатель может развивать мощность, достаточную для движения автомобиля с полной нагрузкой со скоростью 30…40 км/ч, и бензиновый бак. Длительно работать на бензине не разрешается.
Схема газобаллонной установки автомобиля ЗИЛ-138 показана на рис. 32. В нее входят: газовый баллон с арматурой, магистральный вентиль, испаритель газа, газовый фильтр, редуктор, манометр, смеситель, воздушный фильтр, газопроводы. Для работы на бензине имеются карбюратор и бак.
Рис. 32. Схема газобаллонной установки автомобиля ЗИЛ-138:
1 - воздушный фильтр; 2 - трубка подвода воды к испарителю; 3 - шланг высокого давления от испарителя к фильтру газа; 4 - испаритель газа; 5 - шланг подвода воды от испарителя к компрессору; 6 - газопровод системы холостого хода; 7 - шланг высокого давления от магистрального вентиля к испарителю газа; 8 - труба подвода газа к смесителю; 9 - дозирующе-экономайзерное устройство редуктора; 10 - газовый редуктор; 11 - измерительный преобразователь давления газа; 12 - фильтр редуктора; 13 - манометр газового редуктора; 14 - магистральный вентиль; 15 - бензиновый бак; 16 - фильтр; 17 - смеситель газа; 18 - проставка под смеситель; 19 - расходный вентиль паровой фазы; 20 - контрольный вентиль максимального наполнения баллона; 21 - измерительный преобразователь указателя уровня жидкости в баллоне; 22 - предохранительный клапан; 23 - наполнительный вентиль; 24 - расходный вентиль жидкостной фазы; 25 - баллон; 26 - карбюратор; 27 - шланг, соединяющий вакуумные пространства экономайзера и разгрузочного устройства редуктора с впускным трубопроводом двигателя.
Магистральный вентиль предназначен для перекрытия с места водителя подачи газа из баллона к испарителю, газовому редуктору и смесителю.
Испаритель газа преобразует жидкую фазу топлива в газообразную. Газ проходит по каналу в алюминиевом корпусе смесителя, подогревается циркулирующей через полость корпуса водой из системы охлаждения двигателя и испаряется.
Газовый фильтр, оснащенный фильтрующим элементом, состоящим из металлической сетки и пакета войлочных пластин, очищает газ, поступающий к редуктору, от механических примесей - окалины и ржавчины. Фильтр установлен на входном штуцере редуктора.
Редуктор служит для снижения давления, поступающего к смесителю газа до близкого к атмосферному. При остановке двигателя редуктор автоматически прекращает подачу газа к смесителю.
В цилиндрическом корпусе редуктора размещены камера А первой ступени, камера Б второй ступени и кольцеобразная камера В вакуумного разгружателя.
Одна из стенок камеры первой ступени образована резиновой диафрагмой, края которой зажаты между корпусом редуктора и крышкой. Со стороны крышки на диафрагму постоянно давит сжатая пружина, стремящаяся прогибать диафрагму внутрь корпуса редуктора (вверх). Центральная часть диафрагмы связана коленчатым рычагом с клапаном, благодаря чему при прогибании диафрагмы внутрь рычаг открывает клапан, а при прогибании ее наружу закрывает его.
В камере второй ступени находится зажатая по окружности между верхней частью корпуса и крышкой диафрагма. Ее центральная часть соединена рычагом с клапаном второй ступени. Прогибание диафрагмы вниз вызывает открытие клапана второй ступени, прогибание ее вверх - закрытие клапана. Действующая на шток диафрагмы пружина стремится выгибать диафрагму вверх.
Полости под крышками диафрагм камер первой и второй ступеней сообщены с атмосферой, а следовательно, снаружи на обе диафрагмы постоянно действует атмосферное давление.
В камере В разгружателя установлена кольцевая диафрагма, на которую действует пружина, выгибающая диафрагму вверх.
Снизу к корпусу редуктора прикреплен корпус дозирующе-экономайзерного устройства, в котором размещены основное дозирующее устройство редуктора и экономайзер с пневматическим приводом.
В дозирующее устройство входят дозирующие отверстия постоянного и переменного сечения, клапан-регулятор экономической регулировки газовой смеси и регулировочный винт мощностной регулировки. Клапан с пружиной и диафрагма с пружиной являются деталями экономайзера.
Корпус дозирующе-экономайзерного устройства имеет патрубок для выхода газа; штуцеры на крышке корпуса служат для соединения камеры В разгружателя с полостью под диафрагмой экономайзера и с впускным трубопроводом двигателя.
Редуктор крепят под капотом двигателя к передней стенке кабины на специальном кронштейне. Газ к редуктору подводится через газовый фильтр, укрепленный на штуцере. К штуцеру присоединяют трубку манометра, позволяющего контролировать давление в камере первой ступени. Патрубок соединяют газопроводом низкого давления со смесителем, а штуцер при помощи резиновой трубки с впускным трубопроводом двигателя.
Рис. 33. Газовый редуктор:
а -- устройство; б - схема действия; А - камера первой ступени; Б - камера второй ступени; В - камера вакуумного разгружателя; 1 - штуцер подвода газа; 2 - штуцер для присоединения манометра; 3 - клапан первой ступени; 4 и 5 - крышка диафрагмы и диафрагма камеры первой ступени; 6 - пружина диафрагмы первой ступени; 7 - регулировочная гайка; 8 - рычаг привода клапана первой ступени; 9 - клапан второй ступени; 10 - клапан-регулятор; 11 - клапгн экономайзера; 12 - пружина клапана; 13 я 18 - штуцеры; 14 - крышка корпуса
При открывании магистрального вентиля газ из баллона начинает поступать через испаритель, фильтр, газовый фильтр редуктора (рис. 33), входной штуцер и открытый клапан в камеру А первой ступени редуктора. По мере поступления газа давление в камере повышается, и, когда оно достигает требуемой величины (избыточное или манометрическое давление должно быть 0,17…0,18 МПа или 1,7… 1,8 кгс/см2), диафрагма 5 выгибается вниз и рычажный привод закрывает клапан, прекращая доступ газа в редуктор. Если давление в камере первой ступени падает, пружина прогибает диафрагму вверх, клапан открывается и в камеру снова начинает поступать газ. Таким образом, в камере первой ступени автоматически устанавливается постоянное давление, величина которого зависит от силы натяжения пружины.
Предохранительный клапан предотвращает повреждение диафрагмы камеры первой ступени редуктора, которое может произойти вследствие нарушения герметичности закрытия ее клапана. Если клапан камеры первой ступени закрывается неплотно, газ из баллона все время поступает в эту камеру и давление в ней может превысить допустимую величину. Пружина предохранительного клапана отрегулирована на давление ло 0,45 МПа (4,5 кгс/см2). При большем давлении предохранительный клапан открывается и выпускает часть газа из камеры первой ступени наружу.
Пока двигатель не работает, клапан камеры второй ступени закрыт и газ в нее из камеры первой ступени не поступает. При пуске двигателя в камере второй ступени, соединенной газопроводом со смесителем, образуется разрежение, и диафрагма, прогибаясь внутрь, через рычажный привод откроет клапан 9. Газ из камеры первой ступени начнет перетекать в камеру второй ступени, давление в которой по мере поступления в нее газа повышается. Когда давление поднимется до близкого к атмосферному, клапан закроется и поступление газа из камеры первой ступени прекратится.
Действует разгружатель следующим образом. Когда двигатель не работает, давление пружины разгружателя передается через упор на тарелку диафрагмы, увеличивая силу закрытия клапана второй ступени.
Во время работы двигателя на малых частотах холостого хода и при малых нагрузках (дроссель смесителя прикрыт) в камере В разгружателя, соединенной трубкой с впускным трубопроводом двигателя, создается сильное разрежение и диафрагма прогибается вниз. Упор прекращает давление на диафрагму камеры второй ступени, вследствие чего на клапан второй ступени действует только одна пружина, позволяющая ему открываться даже при отсутствии разрежения в камере второй ступени.
Благодаря этому при малых частотах холостого хода и малых нагрузках газ из камеры второй ступени поступает к смесителю под избыточным давлением 100…200 Па (10…20 мм вод. ст.). По мере возрастания нагрузки двигателя давление газа на выходе из редуктора и в камере второй ступени понижается, и в ней создается небольшое разрежение.
Дозирующе-экономайзерное устройство регулирует количество газа, поступающего к смесителю, а следовательно, и поддерживает необходимый состав газовоздушной смеси.
При малых и средних нагрузках двигателя, когда дроссель смесителя открыт не полностью, в задроссельном пространстве смесителя поддерживается значительное разрежение. Поскольку полость под диафрагмой экономайзера сообщена с задроссельным пространством, в ней также образуется разрежение, под действием которого диафрагма прогибается вниз и клапан экономайзера закрывается. На этом режиме газ из камеры второй ступени редуктора проходит к выходному патрубку через отверстие постоянного сечения и отверстие, сечение которого можно изменять вращением клапана-регулятора; положение последнего подбирают с расчетом получения экономичной работы двигателя.
При больших нагрузках, когда открытие дросселя смесителя приближается к полному, разрежение в задроссельном пространстве и в полости под диафрагмой экономайзера уменьшается. Под действием пружины диафрагма выгибается вверх и открывает клапан, после чего к выходному патрубку редуктора начинает поступать дополнительное количество газа через отверстие постоянного сечения и отверстие переменного сечения. Количество дополнительно поступающего газа регулируют вращением винта, добиваясь получения от двигателя максимальной мощности.
Смеситель и карбюратор. Смеситель служит для приготовления смеси газа и воздуха. Смеситель двухкамерный, обе камеры работают одновременно и параллельно на всех режимах.
Рис. 34. Смеситель:
1 - газоподводящий патрубок; 2 - обратный клапан; 3 - воздушная заслонка; 4 - газовая форсунка; 5 - диффузор; 6 и 10 - распыливающие отверстия системы холостого хода; 7 - штуцер подвода газа из камеры второй ступени редуктора; 8 и 9 - регулировочные винты системы холостого хода; 11 - дроссель.
Газ поступает к форсунке от редуктора через патрубок и обратный клапан. В нижней части смесительной камеры расположены распыливающие отверстия системы холостого хода, сечение которых можно изменять при помощи регулировочных винтов.
Смеситель снабжен центробежно-вакуумным ограничителем частоты вращения коленчатого вала двигателя, однотипным с устанавливаемым на карбюраторном двигателе ЗИЛ-130.
Смеситель присоединен к впускному трубопроводу двигателя через проставку, к которой прикреплен карбюратор. Работает смеситель следующим образом.
При пуске кратковременно закрывают воздушную заслонку (рис. 34), чтобы усилить разрежение в диффузоре и вызвать усиленный приток газа через форсунку.
На малых частотах холостого хода газ поступает из редуктора через штуцер к распыливающим отверстиям под действием сильного разрежения, образующегося в зоне за прикрытым дросселем.
Во время работы двигателя под нагрузкой газ поступает в смесительную камеру через форсунку. Состав смеси при этом регулируется дозирующе-экономайзерным устройством газового редуктора.
Когда двигатель работает на газе, воздушная заслонка, дроссель карбюратора и топливный (бензиновый) кран должны быть закрыты.
Если требуется перевести двигатель на бензин, необходимо закрыть магистральный вентиль газобаллонной установки и выработать весь газ из приборов, расположенных после этого вентиля, до остановки двигателя. Затем закрыть обе заслонки смесителя и пустить двигатель на бензине, как обычный карбюраторный двигатель.
Для последующего перехода на газ закрывают топливный (бензиновый) кран и вырабатывают бензин из карбюратора. После этого закрывают воздушную заслонку и дроссель карбюратора и пускают двигатель на газе, предварительно открыв магистральный вентиль. Работа двигателя одновременно на бензине и газе не допускается.
Пускают на газе холодный двигатель при открытом паровом и закрытом жидкостном расходных вентилях баллона. Когда двигатель прогреется, открывают жидкостной и закрывают паровой расходные вентили.
При низких температурах окружающего воздуха, когда пуск холодного двигателя на газе затруднен, рекомендуется сначала пустить и прогреть двигатель на бензине, а затем перевести его на газ, как сказано выше.
Газопроводы и их соединения. Газопроводы высокого давления (от баллона до редуктора) изготовляют из стальных или медных трубок с толщиной стенок около 1 мм и наружным диаметром 10… 12 мм. Газопроводы соединяют с приборами газобаллонной установки при помощи ниппельных соединений.
Газопроводы низкого давления (от редуктора до смесителя) выполняют из тонкостенных стальных труб и газостойких резиновых шлангов большого сечения. Соединяют их стяжными хомутами.
Основные неисправности газобаллонной установки: утечка газа через неплотности соединения; неплотное закрытие вентилей и клапанов; засорение газового фильтра; нарушение регулировки редуктора, вызывающее чрезмерное обогащение или обеднение газовоздушной смеси; нарушение регулировки системы холостого хода смесителя.
Правила безопасного труда на газобаллонных автомобилях. При утечке газ образует с воздухом взрывчатые смеси. В случае попадания на кожу сжиженный газ интенсивно испаряется и может вызвать термические ожоги (обмораживание).
Вдыхание испаренного газа вызывает отравление. Поэтому необходимо внимательно следить за герметичностью всех соединений газобаллонной установки. Значительная утечка обнаруживается на слух (по шипению газа), чтобы обнаружить незначительную утечку, смачивают места соединений мыльной водой. При утечке нельзя ставить автомобиль в закрытое помещение.
Возле автомобиля нельзя пользоваться открытым огнем.
При необходимости подтягивания соединений трубопроводов установки следует предварительно закрыть расходные вентили баллонов и выработать газ до остановки двигателя.
К атегория: - Автомобили и трактора
Газовыми называются карбюраторные двигатели, работающие на газообразном топливе – сжатых и сжиженных газах. Система питания таких двигателей имеет специальное газовое оборудование. Имеется также дополнительная резервная система, обеспечивающая при необходимости работу газового двигателя на бензине.
Горючие газы, используемые в газобаллонных автомобилях, могут быть естественными и искусственными. Естественные (природные) газы добывают из подземных газовых или нефтяных скважин. Искусственные газы являются побочными продуктами, получаемыми на химических или металлургических заводах.
Сжиженными (сжижаемыми) газами называют такие, которые переходят из газообразного состояния в жидкое при нормальной температуре и небольшом давлении. К ним относят смеси углеводородов, получаемых при переработке нефти. Для газобаллонных автомобилей использование сжиженных газов предпочтительнее, чем сжатых.
Сжатыми (сжимаемыми) называют газы, которые при обычной температуре окружающей среды и высоком давлении сохраняют газообразное состояние. Природный газ, применяемый для газобаллонных автомобилей, работающих на сжатых газах, состоит в основном из метана. Можно использовать и промышленные газы: светильный, коксовый и синтез-газ, но нужно помнить, что они содержат окись углерода (СО) и поэтому ядовиты.
Таким образом, газовое топливо применяют в двух видах: сжиженный нефтяной газ и сжатый природный газ. Сжиженный нефтяной газ выпускают двух марок: СПБТЗ и СПБТЛ – смесь пропана и бутана техническая зимняя и летняя. Сжатый природный газ выпускают также двух марок (А и Б), различающихся относительной плотностью газа.
Газобаллонные автомобили, работающие на сжиженных газах, по сравнению с автомобилями, работающими на сжатых газах, имеют следующие преимущества: больше грузоподъемность автомобиля, так как баллоны легче и их число меньше; меньше рабочее давление в газобаллонной установке, и, следовательно, такие системы надежнее и безопаснее; выше теплотворная способность газовоздушной смеси, что способствует увеличению мощности двигателя; больше концентрация тепловой энергии в единице объема, что позволяет увеличить радиус действия автомобиля; проще заправочные станции; проще перевозка сжиженных газов на большие расстояния и различными видами транспорта.
В систему питания двигателя, работающего на газе, входят баллоны для газа, вентили, манометры, газопроводы высокого и низкого давлений, редукторы с дозирующими устройствами и смеситель.
При работе двигателя газ из баллонов через фильтр проходит в редуктор. Из редуктора через дозирующее устройство газ проходит в смеситель, где образуется газовоздушная горючая смесь. Смесь под действием разрежения при такте впуска поступает в цилиндры двигателя. Процесс сгорания смеси и отвода отработавших газов происходит так же, как и в карбюраторных двигателях.
Кроме основной, имеется резервная система питания, обеспечивающая работу двигателя на бензине в необходимых случаях (неисправности системы, израсходован весь газ в баллонах и др.). В резервную систему питания входят топливный бак, топливный фильтр, топливный насос и карбюратор. При этом длительная работа двигателя на бензине не рекомендуется, так как приводит к повышенному износу двигателя.
Страница 1
Газовыми называются двигатели, работающие на газообразном топливе – сжатых и сжиженных газах. Особенностью таких двигателей является их способность работать также и на жидких топливах, например, бензине.
Система питания газовых двигателей имеет специальное газовое оборудование. Предусмотрена также дополнительная резервная система, обеспечивающая при необходимости работу двигателя на бензине.
По сравнению с бензиновыми двигателями газовые модели обычно более экономичны, менее токсичны, работают без детонации в цилиндрах, имеют меньший износ деталей ЦПГ, КШМ и др., срок их службы больше в 1,5–2 раза. Однако полная мощность при =const и прочих одинаковых условиях, снижается на 10–20 %, т.к. теплотворность горючей смеси снижается на 10–20 %. Система питания газовым топливом более пожароопасна, для ее технического обслуживания требуется специальное оборудование.
Применяются две разновидности газовых топлив.
Сжатые газы – газы, которые при обычной температуре окружающего воздуха и высоком давлении (до 20 МПа) сохраняют газообразное состояние. В качестве топлива для газовых двигателей обычно используется природный газ на основе метана.
Сжиженные газы – газы, которые переходят из газообразного состояния в жидкое при нормальной температуре воздуха и относительно небольшом давлении (до 1,6 МПа). Это преимущественно нефтяные газы.
Для газовых двигателей используются сжиженные газы следующих марок: СПБТЗ – смесь пропана и бутана техническая зимняя; СПБТЛ – смесь пропана и бутана техническая летняя; БТ – бутан технический.
Газообразное топливо менее токсично, имеет более высокое октановое число (около 100 и более единиц), дает меньшее нагарообразование в цилиндрах и не разжижает масло в картере двигателя.
В систему питания двигателя, работающего на сжатом газе (рис. 9), входят баллоны 1 для сжатого газа, наполнительный 5, расходный 6 и магистральный 18 вентили, подогреватель 17 газа, манометры высокого 8 и низкого 9 давления, редуктор 11 с фильтром 10 и дозирующим устройством 12, газопроводы высокого 3 и низкого 13 давления, карбюратор-смеситель 14 и трубка 19, соединяющая разгрузочное устройство с впускным трубопроводом двигателя.
Рис. 9. Схема системы питания
двигателя, работающего на сжатом газе:
1 – баллон; 2 – тройник; 3, 13 – газопроводы; 4 – крестовина; 5, 6, 18 – вентили; 7 – топливный бак; 8, 9 – манометры; 10 – газовый фильтр;
11 – газовый редуктор; 12 – дозирующее устройство; 14 – карбюратор-смеситель; 15 – топливопровод; 16 – топливный насос; 17 – подогреватель; 19 – трубка; 20 – двигатель
При работе двигателя вентили 6 и 18 открыты. Сжатый газ из баллонов поступает в подогреватель 17, обогреваемый горячими ОГ или охлаждающей жидкостью двигателя – для исключения замерзания (закупорки) дросселирующих проходных сечений данной газовой системы питания. Из подогревателя газ через фильтр 10 проходит в двухступенчатый газовый редуктор 11, где давление газа снижается до 0,9–1,15 МПа. Из редуктора через дозирующее устройство 12 газ проходит в карбюратор-смеситель 14, где образуется горючая (газовоздушная) смесь. Она под действием вакуума поступает в цилиндры двигателя. Процесс сгорания данной смеси и отвода ОГ происходит аналогично процессам в бензиновом двигателе.
Редуктор 11, кроме уменьшения давления газа, изменяет его количество в зависимости от режима работы двигателя. Указанный редуктор быстро выключает подачу газа при остановке двигателя.
Кроме основной, имеется резервная система питания топливом, обеспечивающая работу двигателя на бензине в необходимых случаях (при неисправности газовой системы, израсходовании газа в баллонах и других случаях). При этом длительная работа двигателя на бензине не рекомендуется, т.к. в резервной системе питания отсутствует воздушный фильтр, что может привести к повышенному износу двигателя. Оптимальные углы Θ опережения зажигания, установленные при использовании газового топлива, чаще всего не соответствуют оптимальным Θ бензинового двигателя.
В резервную систему питания входят топливный бак 7, топливный фильтр, топливный насос 16 и топливопровод 15.
Схема системы питания двигателя, работающего на сжиженном газе, показана на рис. 10.
Рис. 10. Схема системы питания двигателя, работающего на сжиженном газе: 1 – топливный фильтр; 2 – топливный насос; 3 – карбюратор; 4 – смеситель; 5 – испаритель; 6 – газовый фильтр; 7 – дозирующее устройство; 8 – газовый редуктор; 9, 10 – манометры; 11, 13 – вентили; 12 – баллон; 14 – двигатель; 15 – топливный бак
Сжиженный газ под давлением из баллона 12 поступает через расходный 13 и магистральный 11 вентили в испаритель 5, где он подогревается горячей жидкостью системы охлаждения двигателя. Затем газ очищается в фильтре 6, поступает в двухступенчатый редуктор 8, где давление газа снижается до атмосферного. Из редуктора газ через дозирующее устройство 7 проходит в смеситель 4, в котором готовится горючая смесь в соответствии с режимом работы двигателя.
Система питания двигателя автомобиля, работающего на альтернативном топливе
Газовое топливо по сравнению с жидким имеет следующие преимущества:
. высокое октановое число позволяет значительно повысить степень сжатия, следовательно, увеличится экономичность двигателя;
. в результате более полного сгорания газового топлива в отработавших газах содержится меньше токсичных веществ;
. возрастает срок службы двигателя, так как отсутствует конденсация топлива и смыв масла со стенок цилиндров;
. увеличивается срок службы свечей зажигания и глушителя вследствие незначительного нагарообразования.
Автомобили, работающие на альтернативном топливе, имеют следующие недостатки:
. уменьшается мощность двигателя из-за более низкой теплоты сгорания топлива;
. снижается грузоподъемность автомобиля из-за наличия баллонов;
. более трудоемкое техническое обслуживание.
Автомобили могут работать на сжатом или сжиженном газе. В качестве сжатых газов применяют природный газ, метан (давление в баллоне 20 МПа), в качестве сжиженных газов (давление в баллонах 1,6 МПа) — этан, пропан, бутан и др. Газобаллонная установка грузового автомобиля для сжатого газа включает в себя: восемь газовых баллонов, соединенных трубками; двухступенчатый газовый редуктор высокого давления; электромагнитный клапан с газовым фильтром; газопроводы; манометры высокого и низкого давления; подогреватель газа; газовые вентили — наполнительный, баллонный и магистральный; карбюратор-смеситель, приборы резервного топлива.
При работе двигателя подача газа из баллонов в систему подачи топлива происходит через два запорных устройства — расходный вентиль и электромагнитный клапан с газовым фильтром. Перед пуском двигателя открывают расходный вентиль. Манометр должен показать наличие газа в баллонах. Газ по трубопроводу поступает в редуктор, где давление автоматически снижается до 0,1 МПа. По пути к редуктору газ подогревается. Затем газ по шлангу поступает в карбюратор-смеситель для образования газовоздушной смеси и далее в цилиндры двигателя.
Для работы на резервном топливе (бензине) автомобиль имеет топливный бак, фильтр-отстойник, топливный насос, топливопроводы.
Газобаллонная установка, работающая на сжиженном газе, состоит из газовых баллонов, испарителя газа, двухступенчатого газового редуктора, манометров высокого и низкого давления, электромагнитного клапана с газовым фильтром, карбюратора-смесителя, приборов резервного топлива. Газовый баллон снабжен контрольным вентилем уровня жидкости, предохранительным клапаном, указателем уровня жидкости, вентилем расхода газа.
Газобаллонная установка для сжиженного газа: 1 — магистральный вентиль; 2 — манометр баллона; 3 — паровой вентиль; 4 — предохранительный клапан; 5 — баллон для сжиженного газа; 6 — контрольный вентиль; 7 — накопительный вентиль баллона; 8 — указатель уровня сжиженного газа; 9 — жидкостной вентиль; 10 — манометр редуктора;11 — двигатель; 12 — карбюратор; 13 — смеситель газа; 14 — бак для бензина; 15 — газовый редуктор; 16 — испаритель сжиженного газа; 17— штуцер для подвода горячей воды; 18 — штуцер для отвода воды; 19 — кран для слива воды.
Сжиженный газ перед использованием переводят в газообразное состояние. Из баллона жидкий газ при открытом магистральном вентиле поступает через электромагнитный клапан с газовым фильтром к испарителю, где подогревается охлаждающей жидкостью системы охлаждения двигателя. Жидкость испаряется, и в парообразном состоянии газ поступает в фильтр, а затем в двухступенчатый газовый редуктор, где давление газа снижается до 0,1 МПа. Далее газ проходит через дозирующее устройство в карбюратор и при такте впуска поступает в цилиндры двигателя. Газовый манометр показывает давление газа в редукторе.